Precision CNC Turning Services Empower Efficient Industrial Part Production
Release time:
2025-04-22
SEO keywords: CNC turning, CNC machining, CNC lathe, multi-axis linkage system SEO Abstract: CNC turning is the core technology of modern manufacturing industry. It adopts advanced equipment and mature technology to provide stable and reliable customized processing solutions. The main technical advantages include the high precision and consistency of CNC technology, imported CNC lathes with high-precision processing capabilities and multi-axis linkage systems, automated tool compensation technology, material adaptability and integrated molding of complex structures.
As one of the core processes of modern manufacturing, CNC turning is widely used in the manufacture of precision parts in the fields of automobiles, aerospace, medical equipment, etc. with its high precision and high efficiency. As a professional CNC turning service provider, we are committed to providing customers with stable and reliable customized processing solutions through advanced equipment and mature processes.
Core technical advantages of CNC turning
CNC (computer numerical control) technology controls the processing process through digital programming, significantly improving the accuracy and consistency of turning, and meeting the stringent technical requirements of complex parts.
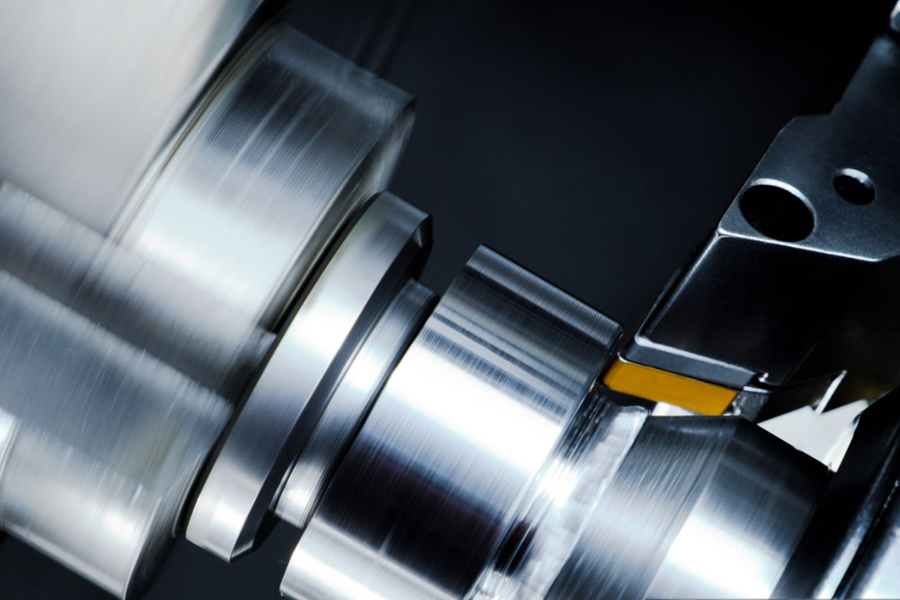
High-precision processing capabilities
Adopting imported CNC lathes and multi-axis linkage systems to achieve micron-level processing accuracy, ensuring that the dimensional tolerances and form and position tolerances of parts such as shafts, sleeves, and threads meet industry standards. Through automated tool compensation technology, reduce manual intervention errors and improve batch production stability.
Wide range of material adaptability
Supports turning of various materials such as stainless steel, aluminum alloy, titanium alloy, engineering plastics, etc., optimizes tool parameters and cooling solutions according to the hardness and cutting characteristics of different materials, avoids deformation, burrs and other problems, and ensures surface finish and yield rate.
Integrated molding of complex structures
Through CAD/CAM software, three-dimensional modeling and path planning can be completed, and complex structures such as stepped shafts, inner cavity threads, and special-shaped curved surfaces can be processed, reducing the precision loss caused by secondary clamping and shortening the multi-process processing cycle.
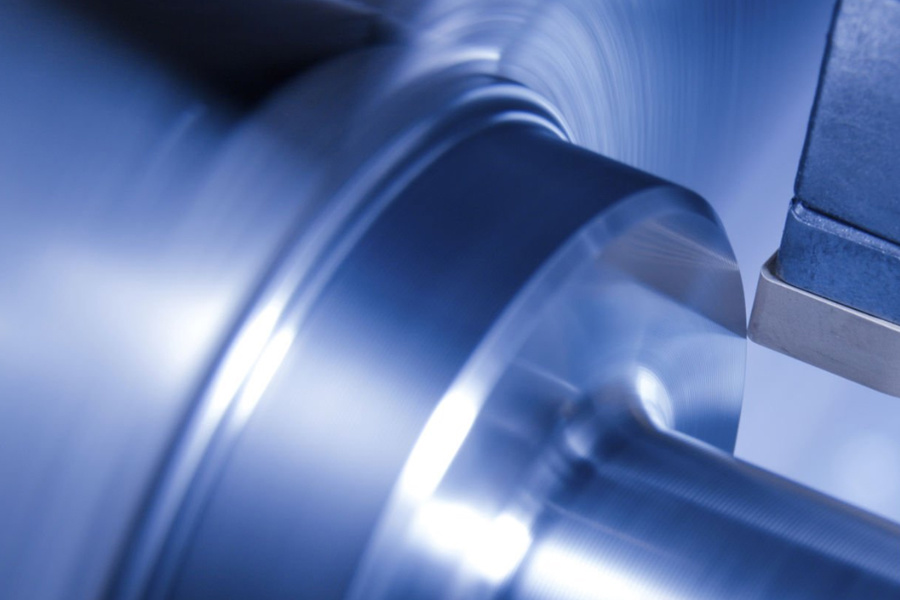
Full-process quality control ensures processing quality
From drawing analysis to finished product delivery, we have established a standardized quality control system to ensure that each batch of parts meets customer technical requirements:
Process pre-examination optimization: The engineering team analyzes the processing difficulties based on the part drawings, and provides feasible suggestions such as structural simplification and tolerance adjustment to reduce processing costs and risks.
Process dynamic monitoring: Real-time monitoring of tool wear, cutting temperature and other parameters during processing, timely adjustment of feed speed and cutting depth to avoid overcutting of materials or tool breakage.
Typical application scenarios of CNC turning
Automotive parts: Precision turning parts such as engine shafts, transmission gears, and hydraulic valve bodies meet the requirements of high temperature and wear resistance.
Medical equipment: Micro high-precision parts such as surgical instruments and implant connectors meet medical-grade cleanliness and biocompatibility standards.
Industrial machinery: core transmission components such as pump bodies, bearing seats, and lead screws to ensure the long-term stability and low failure rate of equipment.
Choose our core value
Technical equipment guarantee: equipped with CNC lathes imported from Germany and Japan, supporting workpiece processing with a diameter of 5mm to 500mm.
Flexible production: supports small-batch trial production and large-scale mass production, and flexibly responds to customers' urgent order needs.
Full-cycle service: provides one-stop services for material procurement, process design, and post-processing (electroplating, anodizing, etc.) to reduce customers' supply chain management costs.
Bowei Machinery has been deeply involved in the field of CNC turning for many years, and provides customers with cost-effective precision processing services with technical accumulation and rigorous attitude. If you need a professional and reliable CNC turning partner, please contact us for technical solutions and quotation support.
Related Products
CNC machining multi-axis linkage accurately processes tooth profile and journal size
CNC machining technology plays a core role in the machining of precision gears and shaft parts, achieving high-precision micron-level precision, significantly improving the wear resistance and fatigue resistance of parts, and ensuring the stable operation and high quality of the transmission system. In modern industrial manufacturing, its application in automobile manufacturing, precision instruments, industrial equipment and other fields has significantly improved the overall quality.
2025-06-28
Automotive precision parts processing: Use high-precision gears to drive the future of new energy
The development of new energy vehicles has put forward higher requirements for the precision of parts. The breakthrough of micron-level manufacturing technology has laid the foundation for the stable operation of the power system. High-precision gears are innovatively applied in the energy conversion system of new energy vehicles, which reduces friction loss, improves transmission efficiency and prolongs gear life.
2025-06-18
The manufacturing process of precision accessories in modern medical equipment, especially the use of core processing technologies such as CNC turning and laser micro-welding to achieve precise manufacturing in complex medical scenarios. These technologies not only require precise dimensional control, but also must meet biocompatibility and long-term stability.
2025-06-14
Five-axis machining centers have gradually become the core equipment for the manufacture of complex parts due to their multi-dimensional dynamic machining capabilities. Compared with four-axis equipment, five-axis machining centers significantly improve the machining accuracy and surface quality of special-shaped structural parts through multi-angle synchronous cutting, shortening the production cycle.
2025-06-11