Optimization selection of workpiece clamping method in CNC lathe machining
Release time:
2025-03-14
The choice of workpiece clamping method is very important in CNC lathe processing, three jaw chuck, four jaw chuck and the center clamping method is commonly used. Among them, the center clamping is suitable for the processing of slender shaft parts, which can ensure the processing accuracy of slender shaft parts to the micron level and meet the high-precision requirements of aviation engines.
In the field of CNC lathe machining, the choice of workpiece clamping method is very important, which directly affects the machining accuracy, efficiency and workpiece quality. Whether it is the strict requirements for precision machining, or the demand for efficient production in machining, optimizing the clamping method is a key link to improve the processing level of CNC lathes.
Three jaw chuck clamping: convenient and efficient universal choice
The three-jaw chuck is one of the most commonly used clamping methods in CNC lathe machining. It has automatic centering function, can quickly clamp round or regular polygon workpiece, easy to operate and high efficiency. In the mass production of small shaft parts or disk parts, the advantage of the three-jaw chuck is obvious. For example, when machining a small motor shaft in cnc milling, the motor shaft is placed into a three-jaw chuck, and the clamping position can be quickly completed, and a certain degree of coaxial accuracy can be guaranteed to meet the processing requirements of general accuracy. This clamping method is suitable for scenarios where the processing accuracy requirements are not particularly high, but the processing efficiency has high requirements, and is widely used in the general machinery manufacturing industry.
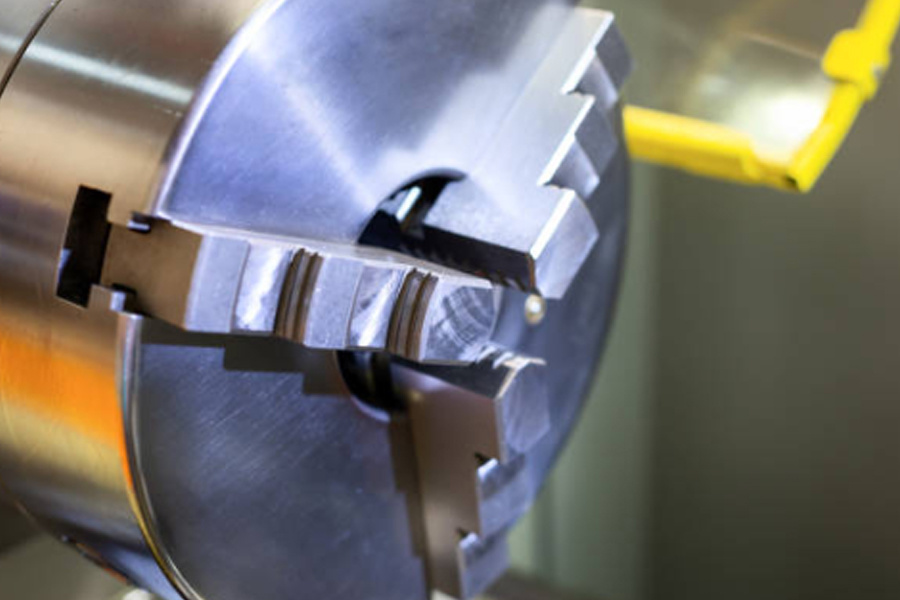
Our jaw chuck clamping: flexible response to irregular workpieces
For irregular, eccentric or non-circular workpieces, four-jaw chucks are a better choice. Each jaw of the four-jaw chuck can be adjusted independently, and by manually adjusting the position of the jaw, various special shapes of the workpiece can be accurately installed. When machining some special-shaped die parts, the four-jaw chuck can flexibly adjust the position of the jaw according to the shape characteristics of the part to achieve firm clamping. However, compared with the three-jaw chuck, the four-jaw chuck clamping requires more debugging time and higher technical requirements for the operator, but it can meet the processing needs of some complex shape workpieces and play an important role in the precision machining of specific special-shaped parts.
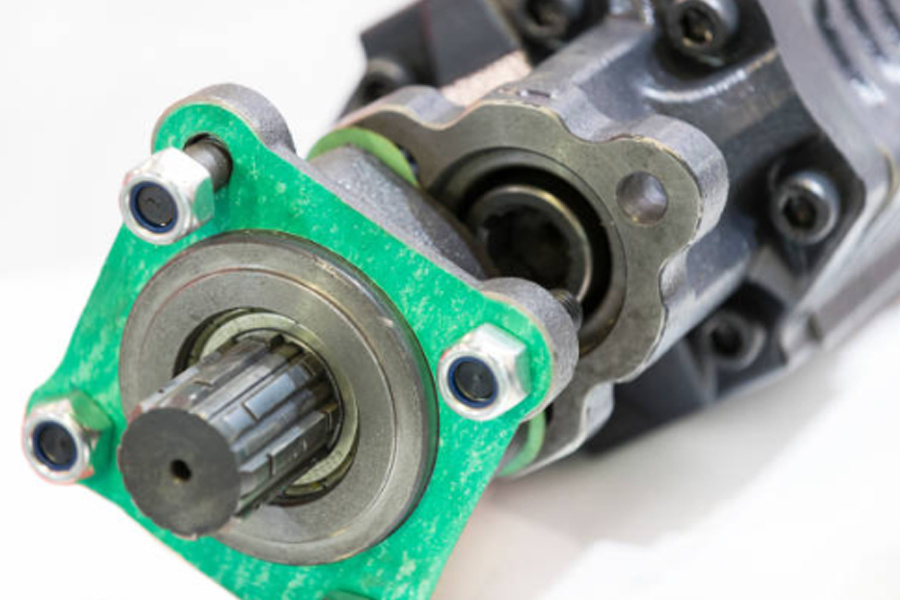
Center clamping: to ensure the machining accuracy of slender shaft parts
When it comes to the processing of slender shaft parts, the center clamping method is favored. When CNC lathe machining slender shaft, due to the poor rigidity of shaft parts, it is easy to deform under the action of cutting force. Using the center clamping, one end is supported by a fixed center, and the other end is matched with an active center, which can effectively limit the axial and radial movement of the workpiece and ensure the stability during the processing. At the same time, with the use of tool holder or center frame, further enhance the rigidity of the workpiece, reduce deformation. When precision machining the slender shaft parts of aeroengines, the center clamping method can ensure the machining accuracy to the micron level, and meet the requirements of high precision parts in the aviation field.
Fixture clamping: customized to improve processing quality
For some mass production and complex shape, high precision requirements of the workpiece, custom fixture clamping is the optimal choice. Through the design of special fixture, according to the shape of the workpiece and processing requirements, accurate positioning and firm clamping can be achieved. When machining complex aerospace parts in the turn-milling complex machining center, the customized fixture can ensure that the workpiece is always in the correct position during the switching of various machining processes, avoid the positioning error caused by multiple installation, and improve the machining accuracy and efficiency. Although the design and production cost of tooling fixtures is high, in mass production, the overall economic benefits can be significantly improved.
The optimal selection of workpiece clamping method in CNC lathe machining needs to consider the shape, size, machining accuracy requirements and production batch. Reasonable selection of clamping methods, whether in different scenarios such as precision machining, machining or cnc milling, can effectively improve processing quality and efficiency, meet the diversified needs of various industries for CNC lathe processing, and promote the continuous development and progress of the manufacturing industry.
Related Products
CNC machining multi-axis linkage accurately processes tooth profile and journal size
CNC machining technology plays a core role in the machining of precision gears and shaft parts, achieving high-precision micron-level precision, significantly improving the wear resistance and fatigue resistance of parts, and ensuring the stable operation and high quality of the transmission system. In modern industrial manufacturing, its application in automobile manufacturing, precision instruments, industrial equipment and other fields has significantly improved the overall quality.
2025-06-28
Automotive precision parts processing: Use high-precision gears to drive the future of new energy
The development of new energy vehicles has put forward higher requirements for the precision of parts. The breakthrough of micron-level manufacturing technology has laid the foundation for the stable operation of the power system. High-precision gears are innovatively applied in the energy conversion system of new energy vehicles, which reduces friction loss, improves transmission efficiency and prolongs gear life.
2025-06-18
The manufacturing process of precision accessories in modern medical equipment, especially the use of core processing technologies such as CNC turning and laser micro-welding to achieve precise manufacturing in complex medical scenarios. These technologies not only require precise dimensional control, but also must meet biocompatibility and long-term stability.
2025-06-14
Five-axis machining centers have gradually become the core equipment for the manufacture of complex parts due to their multi-dimensional dynamic machining capabilities. Compared with four-axis equipment, five-axis machining centers significantly improve the machining accuracy and surface quality of special-shaped structural parts through multi-angle synchronous cutting, shortening the production cycle.
2025-06-11