Comparison and analysis of the core advantages of five-axis machining centers and four-axis machining
Release time:
2025-06-11
Five-axis machining centers have gradually become the core equipment for the manufacture of complex parts due to their multi-dimensional dynamic machining capabilities. Compared with four-axis equipment, five-axis machining centers significantly improve the machining accuracy and surface quality of special-shaped structural parts through multi-angle synchronous cutting, shortening the production cycle.
In the field of precision manufacturing, the five-axis machining center has gradually become the core equipment for the manufacture of complex parts due to its multi-dimensional dynamic machining capabilities. Compared with traditional four-axis equipment, the five-axis machining center realizes the synchronous cutting of multi-angle and multi-surface workpieces through the coordinated movement of the X, Y, Z axes and two rotation axes (A/B/C axes). This technological breakthrough not only expands the freedom of the machining space, but also significantly improves the machining accuracy and surface quality of special-shaped structural parts. Especially in the machining scenarios of complex geometric contours such as aerospace engine blades and medical device joint implants, the five-axis technology reduces the risk of human error by reducing the number of repeated positioning and clamping, while shortening the production cycle. With the growth of the demand for high-precision surface machining, the differences between five-axis and four-axis equipment in terms of the number of linkage axes, machining efficiency and cost control have become the key considerations for enterprise technology upgrade decisions.
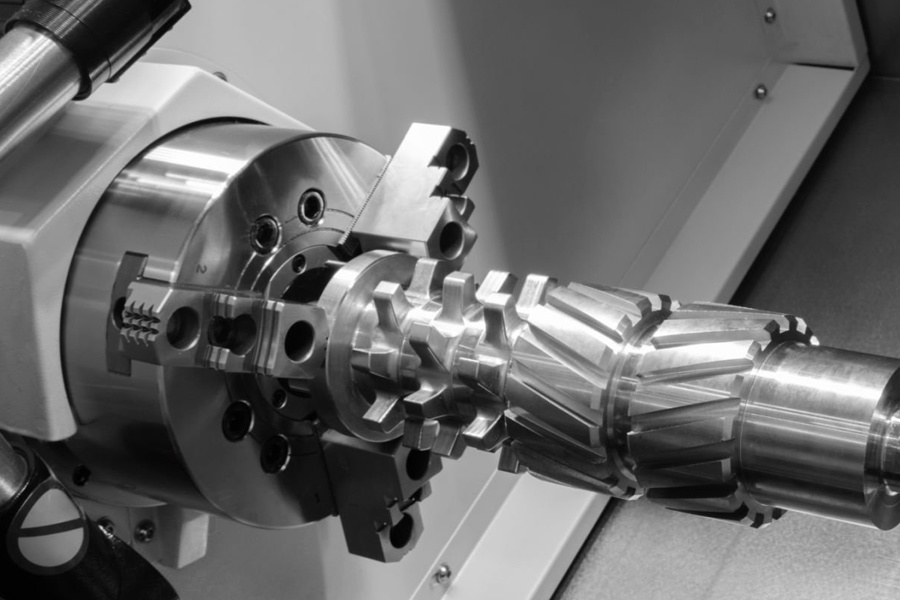
The core competitiveness of the five-axis machining center lies in its multi-dimensional collaborative control capabilities. Through the linkage configuration of the X, Y, Z linear axes and the A, B rotation axes, the equipment can realize the precise planning of the tool space trajectory, so that the cutting point is always perpendicular to the complex surface contour. This multi-angle synchronous processing feature enables special-shaped structural parts such as turbine blades and human bone implants to complete multi-faceted processing through a single clamping, avoiding the cumulative errors caused by multiple positioning in traditional processes. At the same time, the dynamic tool compensation technology of the five-axis system can adjust the tool tip contact angle in real time, maintain a stable cutting load in deep cavity processing or undercut areas, and significantly improve surface finish and tool life. Compared with the limited 3+1 axis motion mode of four-axis equipment, five-axis technology expands the spatial freedom and upgrades the processing range from plane directional engraving to three-dimensional omnidirectional forming, laying a technical foundation for the mass production of high-value-added parts.
Differences between four-axis and five-axis linkage
From the perspective of motion freedom, a four-axis machining center is usually composed of three linear axes (X/Y/Z) and one rotation axis (A or B). Its linkage mode is mainly "three axes + single rotation axis". Multi-angle cutting needs to be achieved through indexing positioning during the processing process. The five-axis equipment integrates two rotary axes (such as A/C or B/C) to form a full-range linkage architecture of "three linear axes + two rotary axes", which enables the tool to maintain normal contact with the workpiece surface at any spatial angle. This difference is particularly significant when processing complex curved surfaces such as turbine blades and spiral bevel gears. The five-axis system adjusts the tool posture in real time to avoid the cutting discontinuity caused by indexing and reversing of four-axis equipment, thereby reducing surface vibration and improving contour accuracy by more than 30%. At the same time, the coordinated movement of the dual rotary axes enables the workpiece to complete five-sided processing in one clamping, reducing the fixture adjustment time by more than 60% compared to the four-axis process.
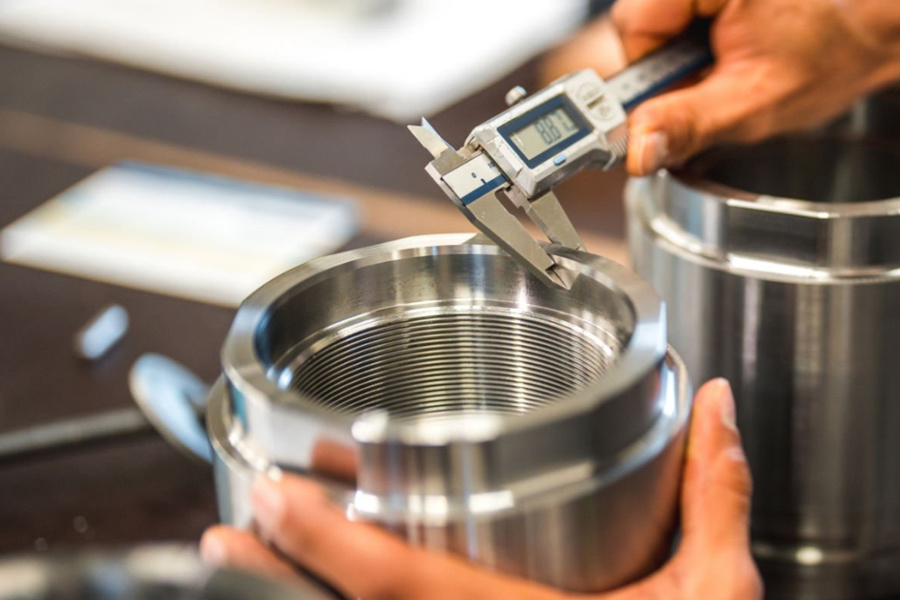
Comparison of complex part processing efficiency
In the complex special-shaped part processing scenario, the five-axis machining center significantly shortens the processing cycle through multi-angle synchronous cutting. The four-axis equipment is limited by the range of motion of the rotary axis. When processing curved surfaces or deep cavity structures, the workpiece clamping angle needs to be adjusted multiple times, resulting in segmented tool paths and increased idle travel. For example, for impeller parts in the aerospace field, four-axis machining requires 3-4 positioning switches, while five-axis equipment uses the compound motion of the B-axis and C-axis to achieve one-time continuous machining of the front and back sides of the blade and the flow channel area, improving overall efficiency by more than 30%. At the same time, the five-axis technology optimizes the tool axis vector control to keep the tool at the optimal cutting angle. In the precision cutting of high-hardness materials such as titanium alloys and high-temperature alloys, a single pass can complete the surface accuracy requirements that four-axis equipment requires multiple processes to achieve, further compressing the ineffective processing time.
Reduce clamping and optimize cost structure
The five-axis machining center significantly reduces the need for repeated positioning of the workpiece through a multi-degree-of-freedom motion system. Compared with the traditional four-axis equipment that requires multiple adjustments to the fixture to complete multi-faceted processing, the five-axis technology can achieve a single clamping to complete the full process of complex curved surfaces. This process improvement not only shortens the auxiliary time by 20%-40%, but also reduces the risk of cumulative errors caused by repeated clamping, and increases the processing qualification rate of precision parts to more than 98%. In the field of medical devices, special-shaped parts such as hip prostheses can reduce more than 5 fixture conversion links through five-axis synchronous cutting, directly reducing labor costs by more than 30% and tool loss by 15%. At the same time, the marginal cost reduction effect brought about by the increase in equipment utilization during mass production reduces the single-piece processing cost of complex structural parts by about 18%-25% compared with the four-axis process.
Overall, the five-axis machining center has shown irreplaceable competitive advantages in the field of complex surface processing through multi-axis linkage and spatial freedom expansion. Compared with four-axis equipment, its synchronous cutting capability not only improves the processing accuracy to the micron level, but also significantly improves the finished product qualification rate of key structural parts by reducing the cumulative error risk caused by multiple clamping. From a cost-effectiveness perspective, the five-axis technology can complete multi-faceted processing through a single clamping, which compresses the production cycle of typical products such as medical device precision components and aircraft engine blades by more than 30%, while reducing the cost of fixture design and manual operation. With the growing demand for the integration of special-shaped parts in industrial manufacturing, five-axis machining centers are gradually becoming the core supporting technology for the manufacturing of high value-added products.
Related Products
CNC machining multi-axis linkage accurately processes tooth profile and journal size
CNC machining technology plays a core role in the machining of precision gears and shaft parts, achieving high-precision micron-level precision, significantly improving the wear resistance and fatigue resistance of parts, and ensuring the stable operation and high quality of the transmission system. In modern industrial manufacturing, its application in automobile manufacturing, precision instruments, industrial equipment and other fields has significantly improved the overall quality.
2025-06-28
Automotive precision parts processing: Use high-precision gears to drive the future of new energy
The development of new energy vehicles has put forward higher requirements for the precision of parts. The breakthrough of micron-level manufacturing technology has laid the foundation for the stable operation of the power system. High-precision gears are innovatively applied in the energy conversion system of new energy vehicles, which reduces friction loss, improves transmission efficiency and prolongs gear life.
2025-06-18
The manufacturing process of precision accessories in modern medical equipment, especially the use of core processing technologies such as CNC turning and laser micro-welding to achieve precise manufacturing in complex medical scenarios. These technologies not only require precise dimensional control, but also must meet biocompatibility and long-term stability.
2025-06-14
Five-axis machining centers have gradually become the core equipment for the manufacture of complex parts due to their multi-dimensional dynamic machining capabilities. Compared with four-axis equipment, five-axis machining centers significantly improve the machining accuracy and surface quality of special-shaped structural parts through multi-angle synchronous cutting, shortening the production cycle.
2025-06-11