Common fault diagnosis and maintenance methods for CNC spindles
Release time:
2025-05-04
Common fault diagnosis and maintenance methods of CNC spindle, including abnormal vibration and excessive heat. Regular lubrication, cleaning and maintenance, reasonable programming, and establishment of maintenance files are the key. Regularly check the tools and replace the worn tools in time to ensure the stable operation of the spindle.
CNC processing technology is essential to contemporary production. Product quality is closely correlated with the reliable functioning of CNC machines, particularly in fields like precision medical component processing and CNC processing of medical parts. The CNC spindle is the most crucial part of the CNC machine and should be operated regularly. Let's discuss typical CNC spindle failure diagnosis and maintenance techniques today.
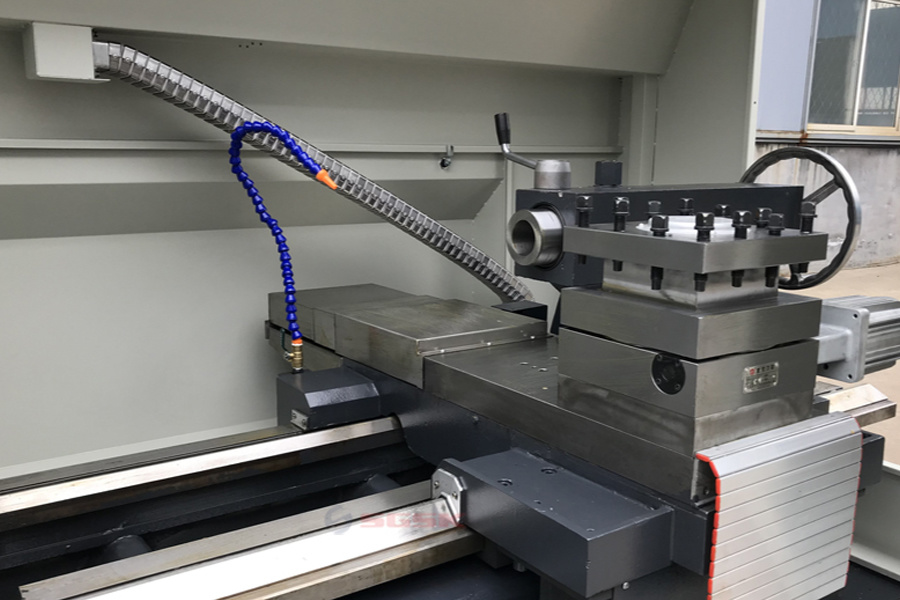
Troubleshooting
Abnormal vibration: The precision of the machining will be significantly impacted when the CNC spindle shakes. This may result in component size variations and make it impossible to fulfill tight medical requirements when producing precision medical parts. The spindle bearing's wear might be the source of the vibration. The raceways or bearing balls will deteriorate with prolonged usage, leading to unsteady operation; this might also be the consequence of tool imbalance. The imbalanced tool will produce centrifugal force while rotating at high speeds. causes vibration. Expert vibration detecting equipment can identify the fault's source by measuring the vibration's frequency and amplitude.
excessive production of heat: The spindle will produce some heat while operating, but if the temperature rises too much, issues might occur. For instance, a too high temperature during CNC precision machining would result in thermal deformation of the spindle components, which will compromise processing accuracy. Common causes include inadequate lubrication, insufficient lubricating oil, or inappropriate lubrication techniques, which are unable to remove heat efficiently. It's also possible that the cutting load is too big, in which case the spindle would produce excessive heat while cutting at high loads continuously. The spindle shell may be touched to feel the temperature, or an infrared thermometer can be used to measure it precisely.
Method of maintenance
The secret to guaranteeing the spindle's regular functioning is regular lubrication. Regularly apply the proper lubricating oil to the spindle in compliance with the equipment manual's specifications to guarantee that all moving parts are completely lubricated, minimize wear, and lower heat production.
Maintenance and cleaning: To prevent dust and cutting chips from getting within the spindle and causing damage, clean it often. Check the spindle cooling system concurrently to make sure there is enough coolant and proper circulation, and promptly remove any contaminants.
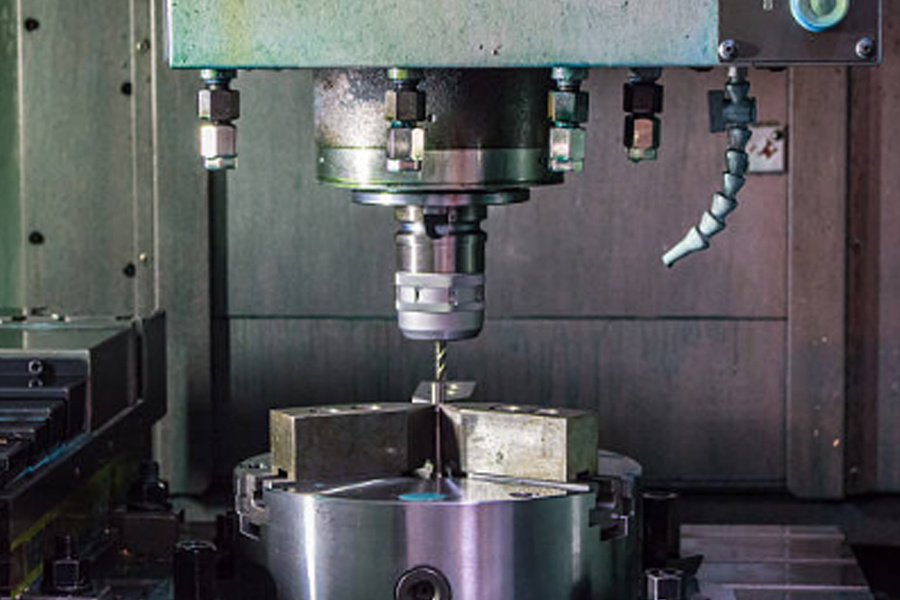
Notes on Using Reasonable Programming: To prevent incorrect cutting parameter setting and excessive spindle load, you should prepare processing programs based on workpiece materials, tools, and other criteria before using CNC processing.
Check the tool frequently: Make sure the tool is balanced and sharp, replace worn-out tools promptly, and avoid spindle failures brought on by tool issues.
Create maintenance files: document the spindle's fault circumstances, maintenance content, and use duration in detail to identify any issues early and create a sensible maintenance schedule.
For CNC machining, particularly for precision medical parts machining and medical parts CNC machining, the steady functioning of CNC spindles is essential. The spindle's service life, processing efficiency, and product quality may all be significantly increased with proper problem detection, efficient maintenance techniques, and sensible usage precautions. In order for CNC machines to better support production, I hope that everyone would pay attention to the maintenance of CNC spindles.
Related Products
CNC machining multi-axis linkage accurately processes tooth profile and journal size
CNC machining technology plays a core role in the machining of precision gears and shaft parts, achieving high-precision micron-level precision, significantly improving the wear resistance and fatigue resistance of parts, and ensuring the stable operation and high quality of the transmission system. In modern industrial manufacturing, its application in automobile manufacturing, precision instruments, industrial equipment and other fields has significantly improved the overall quality.
2025-06-28
Automotive precision parts processing: Use high-precision gears to drive the future of new energy
The development of new energy vehicles has put forward higher requirements for the precision of parts. The breakthrough of micron-level manufacturing technology has laid the foundation for the stable operation of the power system. High-precision gears are innovatively applied in the energy conversion system of new energy vehicles, which reduces friction loss, improves transmission efficiency and prolongs gear life.
2025-06-18
The manufacturing process of precision accessories in modern medical equipment, especially the use of core processing technologies such as CNC turning and laser micro-welding to achieve precise manufacturing in complex medical scenarios. These technologies not only require precise dimensional control, but also must meet biocompatibility and long-term stability.
2025-06-14
Five-axis machining centers have gradually become the core equipment for the manufacture of complex parts due to their multi-dimensional dynamic machining capabilities. Compared with four-axis equipment, five-axis machining centers significantly improve the machining accuracy and surface quality of special-shaped structural parts through multi-angle synchronous cutting, shortening the production cycle.
2025-06-11