Vibration suppression strategy for high-speed milling in CNC milling
Release time:
2025-03-12
High speed milling is an important process of precision machining in modern manufacturing industry, but its vibration problems seriously affect the quality and efficiency of machining. Tool selection and optimization, reasonable design of tool geometry parameters, precise control of cutting parameters, and selection of appropriate tools for machining complex parts are all effective measures to suppress vibration.
In the field of precision machining in modern manufacturing industry, cnc milling has become an indispensable and important process. Among them, high-speed milling is widely used in aerospace, automobile manufacturing and other industries by virtue of its high efficiency and high precision. However, the vibration produced in the process of high-speed milling seriously affects the machining quality and efficiency, so it is very important to explore effective vibration suppression strategies.
Tool selection and optimization
Tools play a key role in cnc milling, and their performance has a direct impact on vibration generation. In high-speed milling, the tool with good rigidity and good dynamic balance should be selected. For example, the use of carbide cutting tools, and the fine dynamic balance of the tool debugging, can effectively reduce the vibration caused by the imbalance of the tool. At the same time, the geometric parameters of rational tool design can not be ignored. Increasing the front Angle of the tool can reduce the cutting force and reduce the vibration. Optimize the blunt radius of the cutting edge of the tool to make it sharper and further reduce the cutting force. When machining complex parts, the right tool can significantly improve machining stability and reduce the risk of vibration.
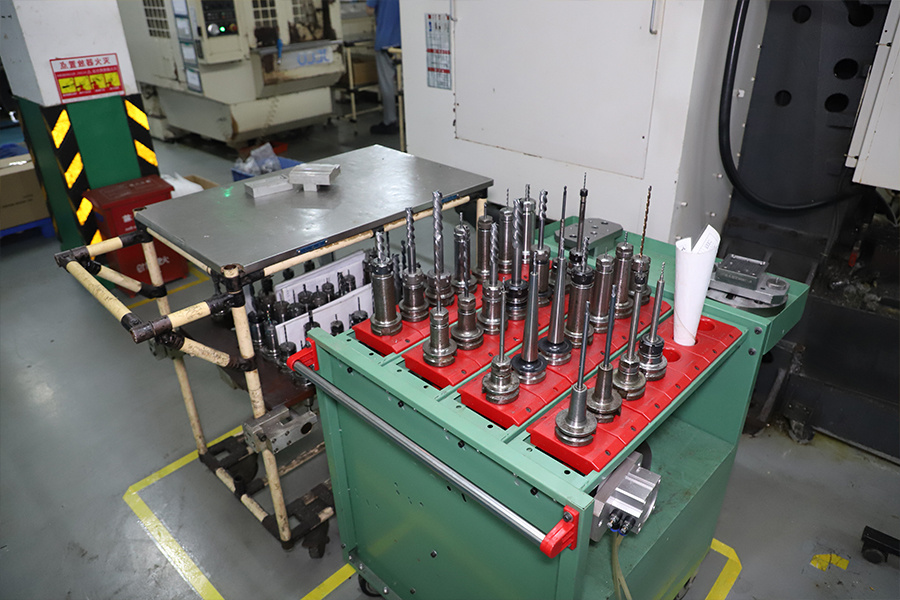
Precise control of cutting parameters
The setting of cutting parameters has significant influence on the vibration of high speed milling. Cutting speed is one of the key parameters, too high or too low cutting speed may cause resonance, resulting in vibration intensification. Through test and simulation analysis, the optimal cutting speed range of the combination of tool and workpiece material is found, which can effectively avoid the resonance zone and restrain vibration. The feed rate and cutting depth also need to be adjusted reasonably. Reducing the cutting depth and increasing the feed can make the cutting force more stable and reduce the vibration. In the actual cnc milling process, according to the workpiece material, tool characteristics and machining requirements, accurate calculation and optimization of cutting parameters is an important means to suppress vibration and ensure machining quality.
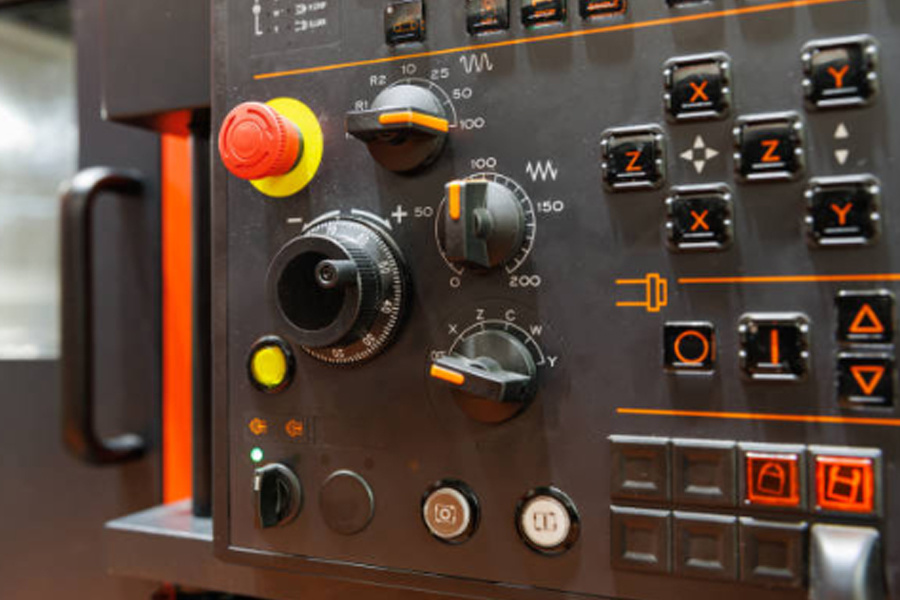
Machine tool structure and system improvement
As the basic equipment of cnc milling, the structure and system performance of machine tool play a decisive role in vibration suppression. Strengthen the structural rigidity of the machine tool, the use of high-rigidity bed, column and other components, can effectively resist the cutting force, reduce the vibration transmission. At the same time, optimize the spindle system of the machine tool, improve the dynamic balance accuracy of the spindle and the stiffness of the bearing, and reduce the vibration of the spindle during high-speed rotation. In addition, an advanced vibration monitoring and control system is introduced to monitor the vibration during milling in real time, and when the vibration exceeds the set threshold, the system automatically adjusts the cutting parameters or takes other suppression measures to ensure the stability of the machining process. In some high-end turn-milling composite machining centers, such advanced vibration suppression systems are equipped, which greatly improves the machining accuracy and efficiency.
In the high-speed milling process of cnc milling, through reasonable selection of tools, accurate control of cutting parameters and improve the structure and system of machine tools and other strategies, can effectively inhibit the generation of vibration, improve processing quality and efficiency, meet the stringent requirements of various industries for precision machining, and promote the manufacturing industry to a higher level.
Related Products
CNC machining multi-axis linkage accurately processes tooth profile and journal size
CNC machining technology plays a core role in the machining of precision gears and shaft parts, achieving high-precision micron-level precision, significantly improving the wear resistance and fatigue resistance of parts, and ensuring the stable operation and high quality of the transmission system. In modern industrial manufacturing, its application in automobile manufacturing, precision instruments, industrial equipment and other fields has significantly improved the overall quality.
2025-06-28
Automotive precision parts processing: Use high-precision gears to drive the future of new energy
The development of new energy vehicles has put forward higher requirements for the precision of parts. The breakthrough of micron-level manufacturing technology has laid the foundation for the stable operation of the power system. High-precision gears are innovatively applied in the energy conversion system of new energy vehicles, which reduces friction loss, improves transmission efficiency and prolongs gear life.
2025-06-18
The manufacturing process of precision accessories in modern medical equipment, especially the use of core processing technologies such as CNC turning and laser micro-welding to achieve precise manufacturing in complex medical scenarios. These technologies not only require precise dimensional control, but also must meet biocompatibility and long-term stability.
2025-06-14
Five-axis machining centers have gradually become the core equipment for the manufacture of complex parts due to their multi-dimensional dynamic machining capabilities. Compared with four-axis equipment, five-axis machining centers significantly improve the machining accuracy and surface quality of special-shaped structural parts through multi-angle synchronous cutting, shortening the production cycle.
2025-06-11