Improvement of CNC lathe machining process for shaft parts
Release time:
2025-03-07
In the field of precision machining, slender shaft parts are widely used in automobile manufacturing and other industries. By optimizing tool selection, reasonably designing tool geometry Angle and cutting parameters, the machining quality and efficiency can be effectively improved, and the deformation risk of parts can be reduced.
In the field of precision machining in modern manufacturing, slender shaft parts are widely used in aerospace, automobile manufacturing and other industries. Such parts require high machining accuracy, and CNC lathes, as important equipment for CNC machining, play a key role in slender shaft machining. By continuously improving the machining process, the machining quality and efficiency can be effectively improved.
Optimize tool selection
The performance of the tool has a significant impact on the machining quality of slender shafts. When machining slender shafts, due to their poor rigidity, they are prone to vibration and deformation, so sharp and wear-resistant tools are required. For example, carbide coated tools can be used, and their coatings can reduce cutting forces and tool wear. When CNC milling the outer cylindrical contours or keyways of slender shafts, the machining accuracy and surface quality can be guaranteed. At the same time, the geometric angles of the tool are reasonably designed, such as increasing the tool rake angle, reducing the cutting force, and reducing the generation of cutting heat, further reducing the risk of part deformation, and ensuring the stability of the machining process.
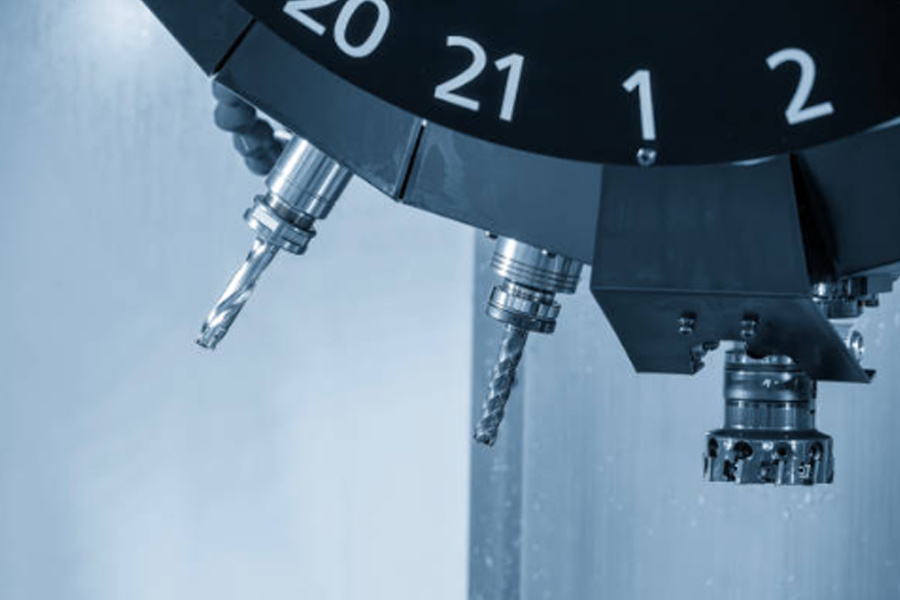
Innovative clamping methods
The traditional clamping method is prone to bending and deformation of parts when machining slender shafts. To solve this problem, a combination of double center clamping and tool rest can be used. Double center clamping can limit the axial and radial movement of the slender shaft and provide stable support. The tool rest is close to the back of the tool to offset the cutting force in real time and prevent the shaft parts from bending due to the cutting force. In actual processing, the clamping stability of the slender shaft can be effectively improved by accurately adjusting the top force of the double center and the support position of the tool rest. In addition, the use of elastic sleeve clamping and the use of the elastic deformation of the sleeve to evenly hold the slender shaft can also reduce the damage to the parts during the clamping process and improve the processing accuracy.
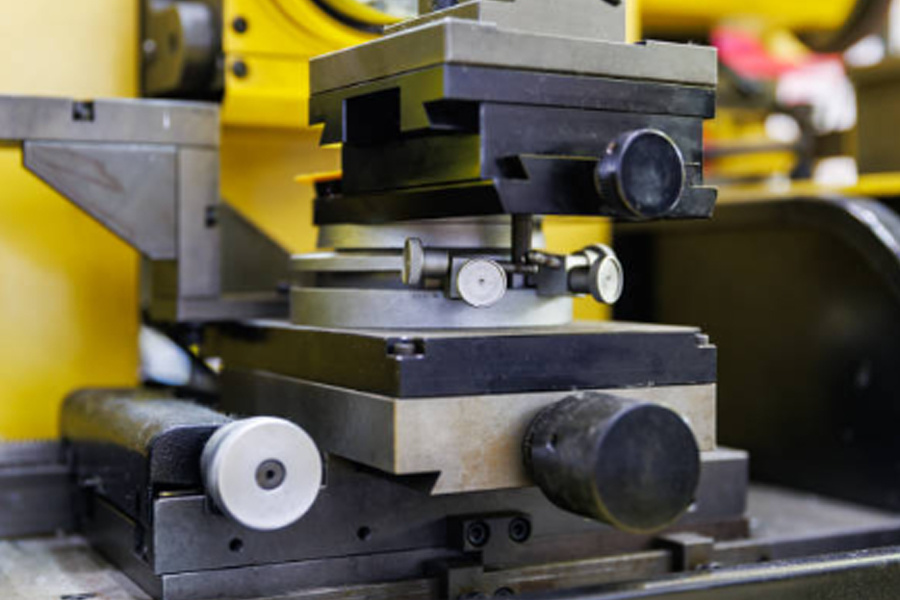
Reasonable adjustment of cutting parameters
The reasonable setting of cutting parameters is the key link in improving the processing technology of slender shafts. When turning slender shafts, the cutting speed should not be too high, otherwise a large amount of cutting heat will be generated, aggravating the deformation of the parts. Appropriately reducing the cutting speed, combined with a larger feed rate and a smaller cutting depth, can reduce the generation of cutting force and cutting heat while ensuring processing efficiency. For example, in CNC lathe processing, according to the material characteristics and size requirements of the slender shaft, the cutting parameters are accurately calculated and adjusted to effectively control the processing accuracy and surface roughness of the parts. At the same time, the cooling and lubricating effects of the cutting fluid are fully utilized to reduce the cutting temperature, reduce tool wear, and further optimize the processing technology.
The process improvement of CNC lathe processing of slender shaft parts involves tool selection, clamping method innovation, and cutting parameter optimization. Through these improvement measures, the processing quality and efficiency can be significantly improved when machining, precision machining, and CNC milling slender shaft parts, meeting the needs of various industries for high-precision slender shaft parts, and promoting the development of the manufacturing industry to a higher level.
Related Products
CNC machining multi-axis linkage accurately processes tooth profile and journal size
CNC machining technology plays a core role in the machining of precision gears and shaft parts, achieving high-precision micron-level precision, significantly improving the wear resistance and fatigue resistance of parts, and ensuring the stable operation and high quality of the transmission system. In modern industrial manufacturing, its application in automobile manufacturing, precision instruments, industrial equipment and other fields has significantly improved the overall quality.
2025-06-28
Automotive precision parts processing: Use high-precision gears to drive the future of new energy
The development of new energy vehicles has put forward higher requirements for the precision of parts. The breakthrough of micron-level manufacturing technology has laid the foundation for the stable operation of the power system. High-precision gears are innovatively applied in the energy conversion system of new energy vehicles, which reduces friction loss, improves transmission efficiency and prolongs gear life.
2025-06-18
The manufacturing process of precision accessories in modern medical equipment, especially the use of core processing technologies such as CNC turning and laser micro-welding to achieve precise manufacturing in complex medical scenarios. These technologies not only require precise dimensional control, but also must meet biocompatibility and long-term stability.
2025-06-14
Five-axis machining centers have gradually become the core equipment for the manufacture of complex parts due to their multi-dimensional dynamic machining capabilities. Compared with four-axis equipment, five-axis machining centers significantly improve the machining accuracy and surface quality of special-shaped structural parts through multi-angle synchronous cutting, shortening the production cycle.
2025-06-11