Application advantages of milling and turning composite machining center
Release time:
2025-03-05
Turning and milling complex machining center is a precision machining equipment in modern manufacturing industry, which has significant processing efficiency improvement and high precision assurance ability. It achieves a high degree of integration of a variety of processing technologies, simplifies the process flow and reduces the production cost. In the processing of complex parts, the turning and milling composite machining center has shown excellent application advantages.
The application advantage of turning and milling complex machining center in the machining of complex parts
In the modern manufacturing industry, the processing demand of complex parts is increasing day by day, and the requirements for processing technology are getting higher and higher. As an advanced CNC machining equipment, the turning and milling complex machining center stands out in the field of precision machining, bringing many significant advantages to the processing of complex parts.
Improve processing efficiency
One of the biggest advantages of the turning and milling complex machining center is that it can significantly improve processing efficiency. Traditional machining often requires multiple equipment and multiple clamping to complete the processing of complex parts. The turning and milling complex machining center integrates a variety of machining functions such as turning and milling in one body, and can complete a variety of processes in a single clamping. For example, in the processing of complex parts such as the impeller of an aeroengine, through the turn-milling complex machining center, operations such as turning the outer circle and milling the blade can be carried out in turn on the same equipment. This not only reduces the time for parts to flow between different equipment, but also avoids the positioning error caused by multiple installations, greatly shortening the overall processing cycle and improving production efficiency.
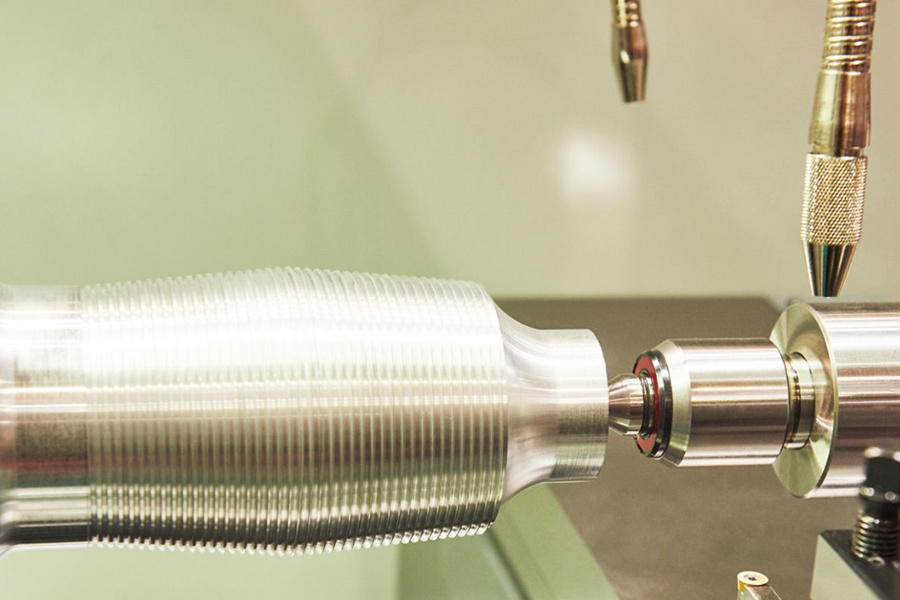
Ensure machining accuracy
Precision is crucial for precision machining. With its advanced CNC system and high-precision moving parts, the turning and milling complex machining center can accurately control the moving path of the tool. When cnc milling machining complex contours, it can precisely cut according to the preset program to ensure the dimensional accuracy and shape accuracy of the parts. Moreover, because a variety of machining is completed in one clamping, the positioning deviation that may be caused by multiple clamping is avoided, and the overall accuracy of the part is further improved. Taking the processing of complex surgical instrument parts in the medical field as an example, the turn-milling complex machining center can control the dimensional error within a very small range, meet the strict requirements for high precision of medical devices, and ensure the quality and safety of medical products.

Enabling process integration
The turning and milling complex machining center achieves a high degree of integration of various machining processes. It can flexibly switch different processes such as turning, milling, drilling and tapping according to the design requirements of the parts. When processing complex mechanical parts, it can complete the processing of multiple features in one processing cycle, such as milling keyway, drilling and other operations after turning the outer circle of shaft parts. This process integration capability not only simplifies the process flow, but also reduces the equipment footprint and the number of operators, reducing production costs. At the same time, due to the reduction of the handover link between different equipment, it also reduces the risk of processing errors caused by human factors.
The turning and milling complex machining center has shown excellent application advantages in the machining of complex parts. Whether in improving processing efficiency, ensuring processing accuracy, or realizing process integration, it has provided strong support for the development of modern manufacturing industry. With the continuous progress of technology, the turning and milling composite machining center will play an important role in more fields, and promote the processing level of complex parts to a new height.
Related Products
CNC machining multi-axis linkage accurately processes tooth profile and journal size
CNC machining technology plays a core role in the machining of precision gears and shaft parts, achieving high-precision micron-level precision, significantly improving the wear resistance and fatigue resistance of parts, and ensuring the stable operation and high quality of the transmission system. In modern industrial manufacturing, its application in automobile manufacturing, precision instruments, industrial equipment and other fields has significantly improved the overall quality.
2025-06-28
Automotive precision parts processing: Use high-precision gears to drive the future of new energy
The development of new energy vehicles has put forward higher requirements for the precision of parts. The breakthrough of micron-level manufacturing technology has laid the foundation for the stable operation of the power system. High-precision gears are innovatively applied in the energy conversion system of new energy vehicles, which reduces friction loss, improves transmission efficiency and prolongs gear life.
2025-06-18
The manufacturing process of precision accessories in modern medical equipment, especially the use of core processing technologies such as CNC turning and laser micro-welding to achieve precise manufacturing in complex medical scenarios. These technologies not only require precise dimensional control, but also must meet biocompatibility and long-term stability.
2025-06-14
Five-axis machining centers have gradually become the core equipment for the manufacture of complex parts due to their multi-dimensional dynamic machining capabilities. Compared with four-axis equipment, five-axis machining centers significantly improve the machining accuracy and surface quality of special-shaped structural parts through multi-angle synchronous cutting, shortening the production cycle.
2025-06-11