Why must medical parts choose ISO 13485 certified CNC service providers?
Release time:
2025-03-10
Choose a CNC service provider with ISO 13485 certification to ensure high-quality production of medical parts, comply with industry standards, establish a risk management system, and pursue excellent quality.
In the medical industry, the quality of medical parts is directly related to the life, health and safety of patients. CNC machining plays a key role in the manufacture of medical parts, and it is particularly important to choose a CNC service provider with ISO 13485 certification.
Quality Assurance: Medical Parts Cannot Be Failed
Medical parts have extremely high requirements for precision and quality. Taking precision machining as an example, when manufacturing key medical parts such as heart stents and artificial joints, the error must be controlled within a very small range. ISO 13485 certification is a standard for the quality management system of medical devices. CNC service providers who have obtained this certification have strict specifications in terms of equipment, process and personnel management. They have advanced CNC machining equipment, such as high-precision CNC milling machining centers, which can ensure the dimensional accuracy and surface quality of parts machining. At the same time, the machining process is monitored throughout the process, from raw material procurement to finished product delivery, every link is strictly controlled to minimize the defective rate and provide solid guarantees for the high-quality production of medical parts.
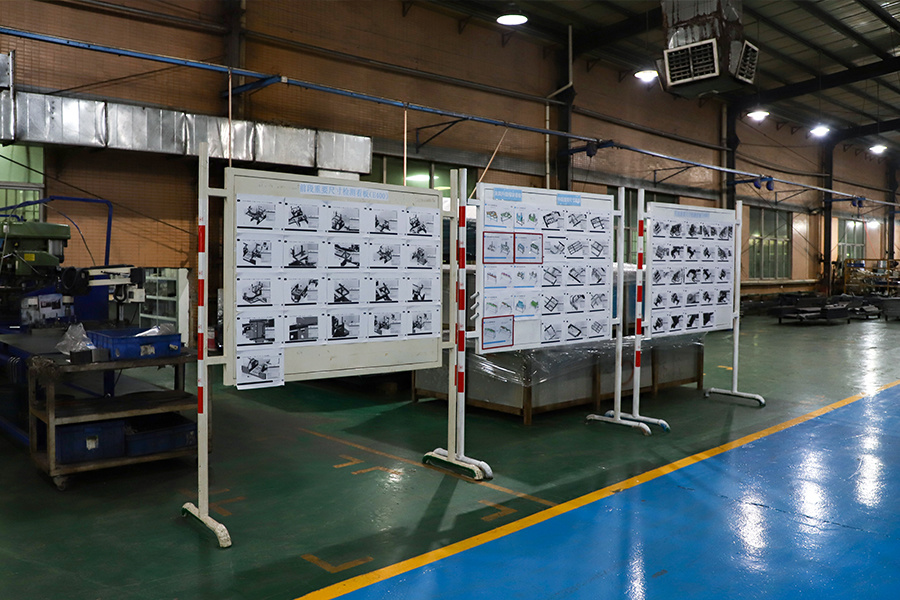
Regulatory Compliance: Strictly Abide by Industry Guidelines
The medical industry is subject to strict regulatory supervision. ISO 13485 certification ensures that CNC service providers comply with international medical device regulations. In the process of machining medical parts, compliance with regulations means ensuring the safety and effectiveness of the parts from the source. For example, for medical parts that come into direct contact with the human body, the selection and processing of materials must comply with relevant hygiene standards. Service providers who have passed ISO 13485 certification are familiar with the details of various regulations and can produce in accordance with the requirements to avoid product recalls or legal disputes due to illegal operations. This is crucial for medical device manufacturers and can effectively reduce legal risks and ensure the normal operation of the company.
Risk management: dealing with potential hidden dangers
There are many potential risks in the production process of medical parts, such as equipment failure and human error. ISO 13485 certification requires service providers to establish a complete risk management system. In complex processes such as milling and turning, the risks that may arise are identified and evaluated in advance. For example, by regularly maintaining equipment, the risk of processing deviations caused by equipment failure is reduced; strict training of operators is carried out to reduce human errors. This forward-looking risk management can detect and solve problems in a timely manner, ensure the stability and continuity of medical parts production, and provide support for the reliable supply of medical equipment.
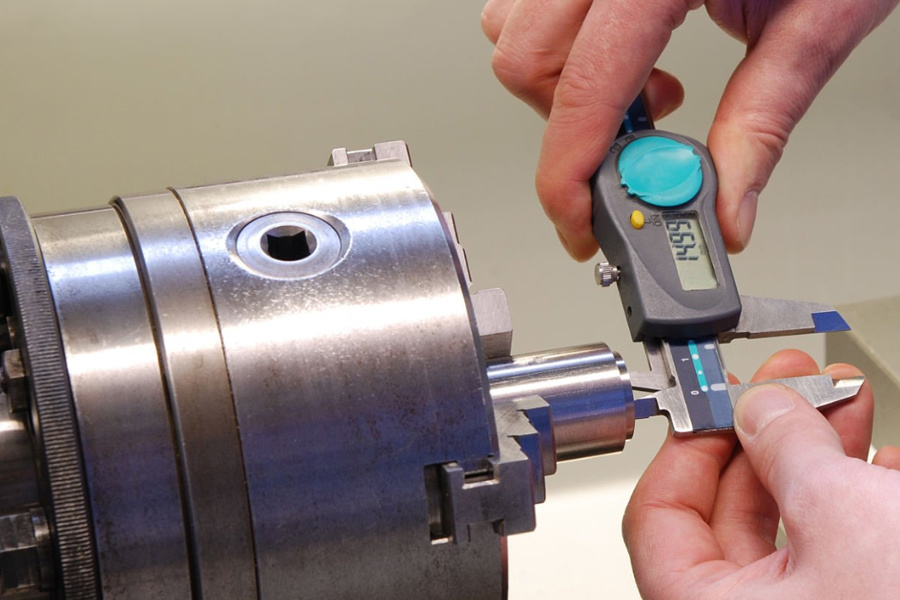
Continuous improvement: pursuit of excellent quality
Obtaining ISO 13485 certification is not a one-time thing, but means that service providers need to continuously improve their quality management systems. In the fierce market competition, this has prompted CNC service providers to continuously optimize processing technology and improve production efficiency. For example, constantly explore new cutting parameters to shorten processing time and reduce costs while ensuring quality. At the same time, actively introduce new technologies and equipment to improve their own processing capabilities, provide better and more efficient services to medical device manufacturers, and promote the entire medical parts processing industry to a higher level.
The particularity of medical parts determines that they must choose ISO 13485 certified CNC service providers. From quality assurance, regulatory compliance, risk management to continuous improvement, every aspect is closely related to the production of medical parts. Only in this way can the safety and reliability of medical equipment be ensured and the health of patients be protected.
Related Products
CNC machining multi-axis linkage accurately processes tooth profile and journal size
CNC machining technology plays a core role in the machining of precision gears and shaft parts, achieving high-precision micron-level precision, significantly improving the wear resistance and fatigue resistance of parts, and ensuring the stable operation and high quality of the transmission system. In modern industrial manufacturing, its application in automobile manufacturing, precision instruments, industrial equipment and other fields has significantly improved the overall quality.
2025-06-28
Automotive precision parts processing: Use high-precision gears to drive the future of new energy
The development of new energy vehicles has put forward higher requirements for the precision of parts. The breakthrough of micron-level manufacturing technology has laid the foundation for the stable operation of the power system. High-precision gears are innovatively applied in the energy conversion system of new energy vehicles, which reduces friction loss, improves transmission efficiency and prolongs gear life.
2025-06-18
The manufacturing process of precision accessories in modern medical equipment, especially the use of core processing technologies such as CNC turning and laser micro-welding to achieve precise manufacturing in complex medical scenarios. These technologies not only require precise dimensional control, but also must meet biocompatibility and long-term stability.
2025-06-14
Five-axis machining centers have gradually become the core equipment for the manufacture of complex parts due to their multi-dimensional dynamic machining capabilities. Compared with four-axis equipment, five-axis machining centers significantly improve the machining accuracy and surface quality of special-shaped structural parts through multi-angle synchronous cutting, shortening the production cycle.
2025-06-11