Intelligent machining types: application scope and technical points of sheet metal cutting
Release time:
2025-05-08
Sheet metal cutting has a fairly broad variety of applications. It is an essential component of the automobile industry. Sheet metal cutting technology can precisely process the sheets into the necessary shapes and sizes, producing high-quality parts for vehicle assembly. vehicle manufacturing is inextricably linked to a variety of sheet metal components.
With its distinct benefits, sheet metal cutting is a crucial technology in many industries in the current era of intelligent machining. Because of its great efficiency and accuracy, sheet metal cutting has emerged as one of the key methods of sheet metal formation.
Sheet metal cutting has a fairly broad variety of applications. It is an essential component of the automobile industry. Sheet metal cutting technology can precisely process the sheets into the necessary shapes and sizes, producing high-quality parts for vehicle assembly. vehicle manufacturing is inextricably linked to a variety of sheet metal components. The sheet metal cutting procedure may be used to the car's body panels, chassis, or mechanical components. For instance, sheet metal cutting may be used to precisely shape steel and other plates throughout the chassis's manufacturing process in order to satisfy the structural specifications. However, the manufacturing of commercial vehicle components also heavily relies on sheet metal cutting. Stronger and longer-lasting components are often needed for commercial vehicles. Sheet metal cutting offers dependable components support for commercial vehicles by enabling the sheets to be cut into a variety of intricate forms in accordance with design specifications.
In the global industrial sector, sheet metal manufacture has a significant position, and one of China's key competitive advantages is its cutting technology. As science and technology continue to progress, sheet metal cutting technology is also continuously evolving and improving. High-precision, high-speed cutting is possible with advanced CNC sheet metal cutting technology, significantly increasing production efficiency and product quality. Companies that manufacture sheet metal also prioritize talent training and technological research and development, and they consistently raise their own technical proficiency and capacity for innovation.
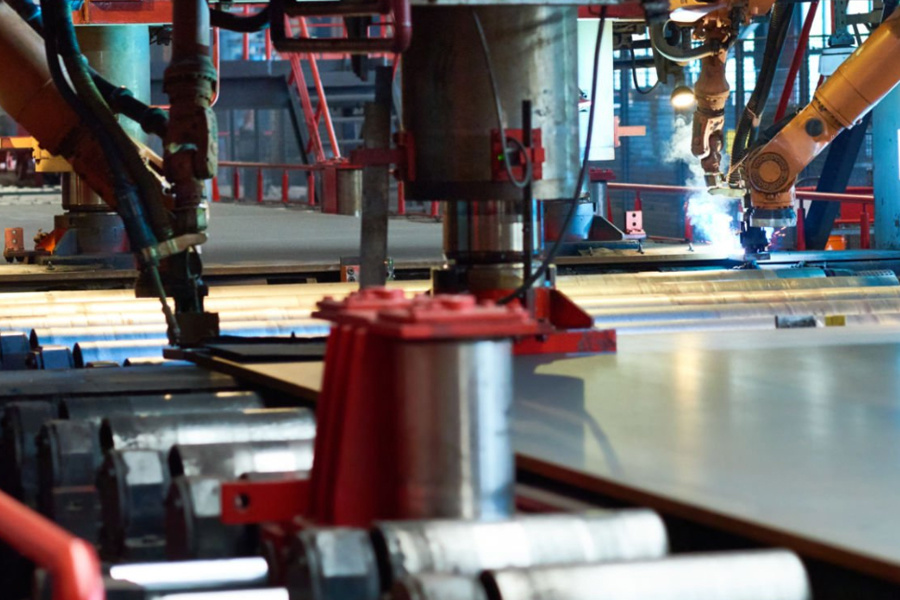
There are several technical details to consider while cutting sheet metal:
1. Choosing the right cutting tools is essential. The right cutting equipment must be chosen based on the particular processing requirements since various cutting equipment works best with different materials and thicknesses. For instance, plasma cutting equipment is appropriate for thicker plates and offers benefits like low cost and fast cutting speed, while laser cutting equipment is ideal for thin plate materials with high cutting accuracy requirements due to its high precision, high speed, and small heat-affected zone.
2. Another crucial step is establishing the cutting settings. Cutting quality and efficiency are directly impacted by the appropriate setup of parameters including cutting speed, power, and gas pressure. In practical use, adjustments must be made based on variables including the plate's material, thickness, and cutting equipment's performance.
3. The plate's location and fastening are also crucial. To guarantee precision and stability throughout the cutting process, the plate has to be securely fastened to the workbench. In addition to lowering the quality of the cut, moving or shaking sheet metal might result in safety incidents.
Strict quality inspection is also necessary to guarantee the quality of sheet metal cutting. Dimension measuring, hardness testing, and appearance inspection are examples of common quality inspection techniques. Dimension measurement is used to make sure that the size of the parts after cutting satisfies design specifications; hardness testing is used to determine whether the material's hardness changes after cutting; and appearance inspection primarily verifies that the cutting surface is smooth and free of burrs, cracks, and other flaws. To guarantee product quality, issues may be found and resolved quickly with rigorous quality inspection.
Sheet metal cutting, one of the key forms of intelligent mechanical processing, has many potential uses in the commercial vehicle and automotive industries, among other sectors. Companies that manufacture sheet metal should always raise the bar for cutting technology, become experts in important technical areas, and provide the world's industrial sector with high-quality sheet metal goods. Simultaneously, as science and technology continue to progress, sheet metal cutting technology will also continue to innovate and grow, strengthening the industrial sector's intelligent and effective growth.
Related Products
CNC machining multi-axis linkage accurately processes tooth profile and journal size
CNC machining technology plays a core role in the machining of precision gears and shaft parts, achieving high-precision micron-level precision, significantly improving the wear resistance and fatigue resistance of parts, and ensuring the stable operation and high quality of the transmission system. In modern industrial manufacturing, its application in automobile manufacturing, precision instruments, industrial equipment and other fields has significantly improved the overall quality.
2025-06-28
Automotive precision parts processing: Use high-precision gears to drive the future of new energy
The development of new energy vehicles has put forward higher requirements for the precision of parts. The breakthrough of micron-level manufacturing technology has laid the foundation for the stable operation of the power system. High-precision gears are innovatively applied in the energy conversion system of new energy vehicles, which reduces friction loss, improves transmission efficiency and prolongs gear life.
2025-06-18
The manufacturing process of precision accessories in modern medical equipment, especially the use of core processing technologies such as CNC turning and laser micro-welding to achieve precise manufacturing in complex medical scenarios. These technologies not only require precise dimensional control, but also must meet biocompatibility and long-term stability.
2025-06-14
Five-axis machining centers have gradually become the core equipment for the manufacture of complex parts due to their multi-dimensional dynamic machining capabilities. Compared with four-axis equipment, five-axis machining centers significantly improve the machining accuracy and surface quality of special-shaped structural parts through multi-angle synchronous cutting, shortening the production cycle.
2025-06-11