Common Fault Diagnosis and Maintenance Methods of CNC Spindle
Release time:
2025-05-02
Vertical, horizontal and gantry CNC machine tools each have their own advantages and disadvantages. Vertical machine tools are easy to operate and occupy a small area, but the processing accuracy and surface quality are low. Horizontal machine tools have high stability and high processing accuracy, but they are greatly affected by gravity when processing large parts. Gantry CNC machine tools have a large processing range, but they are strong in rigidity and require a solid gantry structure.
Selecting the right CNC machine is essential in the field of CNC machining as it has a direct impact on production costs, product quality, and machining efficiency. The three common CNC machine tools—vertical, horizontal, and gantry—each have special benefits and are appropriate for various machining applications.
CNC machine that is vertical
The vertical CNC machine has some clear features because of its spindle, which is positioned perpendicular to the worktable.
Simple to use: The operator can readily monitor and modify the machining process since it is simple to see where the tool and the workpiece are located. This makes it particularly user-friendly for beginners.
Little footprint: For certain businesses with limited space, the vertical CNC machine is a viable option because of its tiny size and compact design.
Field of application: Dental implants, tiny surgical equipment, and other small, accurate components are often processed using vertical CNC machine tools in the CNC machining of medical parts. It can satisfy these components' exacting specifications for surface quality and accuracy. Additionally, vertical CNC machine tools are commonly employed in the processing of tiny components in sectors like watches and electronics.
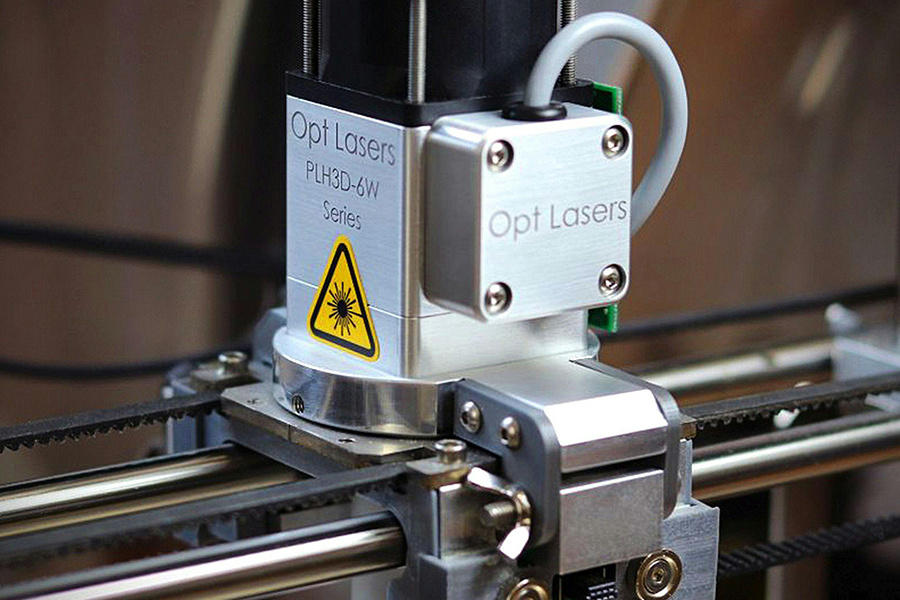
CNC machine tools that are horizontal
Horizontal CNC machine tools vary from vertical machine tools in that their spindle is positioned horizontally.
High stability: The machine tool's horizontal construction increases stability when processing, enables it to sustain high cutting pressures, and makes it appropriate for handling heavy and big workpieces.
High processing precision: Horizontal CNC machine tools perform well in processing accuracy, particularly in axial accuracy, since gravity has less of an impact on tools and workpieces.
Areas of application: Horizontal CNC machine tools are often used in the automotive industry to process huge items like gearbox housings and engine cylinder blocks. Large structural components of planes may also be processed using it in the aerospace industry. These workpieces have very high accuracy requirements in addition to their size. These demands may be effectively satisfied by horizontal CNC machine tools.
CNC gantry machine tools
The distinctive gantry construction of gantry CNC machine tools offers unmatched benefits for processing big workpieces.
Wide processing range: The gantry machine tool's worktable and crossbeam may be made very big, allowing it to process enormous workpieces like bridge components and large molds.
Strong rigidity: The machine tool's very stiff gantry construction efficiently reduces vibration and deformation during processing, ensuring processing precision.
Field of application: Large injection molds, die-casting molds, and other molds are often processed using gantry CNC machine tools in the mold production sector. Large mechanical components are also processed using it in the production of heavy machines. Gantry CNC machine tools may also be useful for certain big medical equipment pieces that need to be processed with a high degree of accuracy.
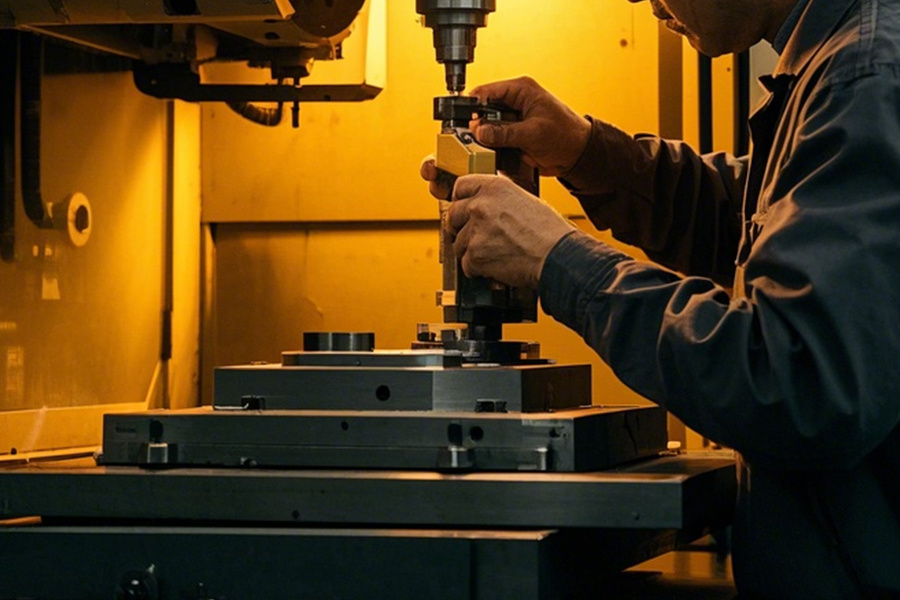
A thorough evaluation of the workpiece's dimensions, shape, accuracy requirements, and processing batch is necessary when selecting an appropriate CNC machine tool. Gantry CNC machine tools are the preferred option for processing big workpieces; horizontal CNC machine tools work well for processing large, high-precision workpieces; and vertical CNC machine tools are appropriate for processing tiny precision components. Only by selecting the appropriate CNC machine tool can you accomplish double the results with half the work in CNC machining and realize accurate and efficient production in many industries, including the CNC machining of medical components.
Related Products
CNC machining multi-axis linkage accurately processes tooth profile and journal size
CNC machining technology plays a core role in the machining of precision gears and shaft parts, achieving high-precision micron-level precision, significantly improving the wear resistance and fatigue resistance of parts, and ensuring the stable operation and high quality of the transmission system. In modern industrial manufacturing, its application in automobile manufacturing, precision instruments, industrial equipment and other fields has significantly improved the overall quality.
2025-06-28
Automotive precision parts processing: Use high-precision gears to drive the future of new energy
The development of new energy vehicles has put forward higher requirements for the precision of parts. The breakthrough of micron-level manufacturing technology has laid the foundation for the stable operation of the power system. High-precision gears are innovatively applied in the energy conversion system of new energy vehicles, which reduces friction loss, improves transmission efficiency and prolongs gear life.
2025-06-18
The manufacturing process of precision accessories in modern medical equipment, especially the use of core processing technologies such as CNC turning and laser micro-welding to achieve precise manufacturing in complex medical scenarios. These technologies not only require precise dimensional control, but also must meet biocompatibility and long-term stability.
2025-06-14
Five-axis machining centers have gradually become the core equipment for the manufacture of complex parts due to their multi-dimensional dynamic machining capabilities. Compared with four-axis equipment, five-axis machining centers significantly improve the machining accuracy and surface quality of special-shaped structural parts through multi-angle synchronous cutting, shortening the production cycle.
2025-06-11