Application and effect analysis of micro-lubrication technology in precision machining
Release time:
2025-02-28
Tool coating is a key factor in improving machining quality. It can significantly reduce the friction coefficient between the tool and the workpiece and increase the service life of the tool. At the same time, it has good wear resistance and corrosion resistance, and can effectively protect the tool matrix.
In the field of precision machining, how to achieve efficient and environmentally friendly production while ensuring machining accuracy and quality has always been the focus of the industry. The emergence of micro-lubrication technology provides an effective solution to this problem and plays an important role in various processes such as CNC machining, milling and turning, and precision machining.
Principle of micro-lubrication technology
Micro-lubrication technology, referred to as MQL (Minimum Quantity Lubrication), is a lubrication method that mixes a very small amount of lubricant (usually a few milliliters per hour) with compressed air and sprays it into the machining area. This technology abandons the traditional lubrication mode of using a large amount of cutting fluid. By precisely controlling the amount of lubricant, it forms an extremely thin lubricating film between the tool and the workpiece, and between the tool and the chips. This lubricating film can not only effectively reduce the friction coefficient and reduce the cutting force, but also play a certain cooling role, thereby improving the machining conditions.
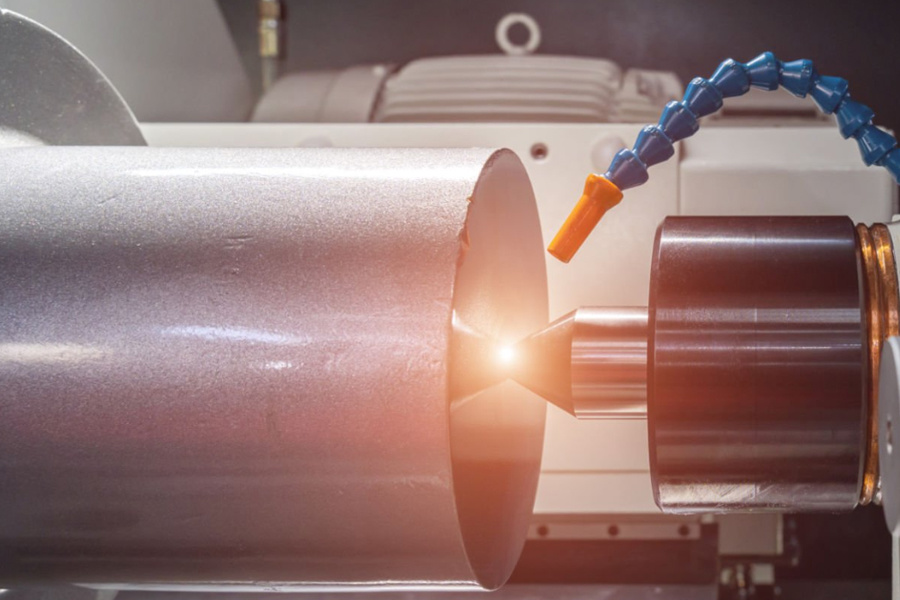
Application of micro-lubrication technology in precision machining
- CNC milling: When CNC milling complex parts, the contact state between the tool and the workpiece is complex, and it is easy to generate a lot of cutting heat and friction. Using micro-lubrication technology to precisely spray lubricants onto the cutting edge of the tool can significantly reduce tool wear. For example, when processing aviation aluminum alloy parts, micro-lubrication can enable the tool to maintain good cutting performance under high-speed cutting, ensure the flatness and finish of the processed surface, and meet the high-precision requirements of aviation parts.
- Turning and milling composite processing: Turning and milling composite processing combines multiple processing technologies such as turning and milling, and the processing process is more complicated. Micro-lubrication technology can adapt to this multi-process switching processing environment and provide effective lubrication at different processing stages. When performing turning and milling composite processing on precision shaft parts, micro-lubrication can reduce tool wear during the conversion process of turning and milling, and ensure the dimensional accuracy and surface quality of the parts.
- Precision machining: In precision machining, the requirements for machining accuracy and surface quality are extremely high. Micro-lubrication technology can effectively reduce vibration and scratches during machining, and avoid corrosion and other problems caused by residual cutting fluid. When manufacturing precision parts such as optical lens molds, micro-lubrication technology can ensure that the roughness of the mold surface reaches an extremely low level, providing a guarantee for the subsequent high-precision manufacturing of lenses.
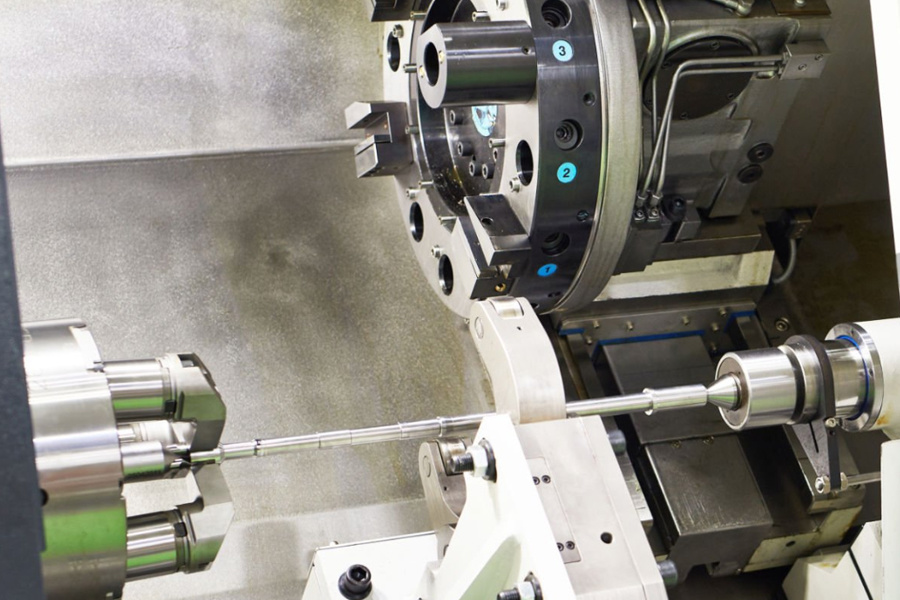
Effect analysis of micro-lubrication technology
- Improve processing efficiency: Since micro-lubrication reduces cutting force and tool wear, the service life of the tool can be extended, the number of tool changes is reduced, and the processing efficiency is improved. At the same time, fast chip discharge also contributes to continuous processing.
- Improve processing quality: By forming a good lubrication film, micro-lubrication effectively reduces surface roughness, ensures dimensional accuracy and shape accuracy, and makes the processed surface smoother and more uniform.
- Environmental protection and energy saving: Micro-lubrication technology greatly reduces the use of cutting fluid, reduces the cost of purchasing, storage, and processing of cutting fluid, and reduces pollution to the environment, which is in line with the concept of sustainable development.
Micro-lubrication technology has a wide range of application prospects and significant effects in precision machining. Whether in CNC milling, turning and milling composite machining or precision machining, it can bring many benefits to the machining process. With the continuous development and improvement of technology, micro-lubrication technology will play a more important role in the field of precision machining, and promote the industry to develop in the direction of high efficiency, environmental protection and precision.
Related Products
CNC machining multi-axis linkage accurately processes tooth profile and journal size
CNC machining technology plays a core role in the machining of precision gears and shaft parts, achieving high-precision micron-level precision, significantly improving the wear resistance and fatigue resistance of parts, and ensuring the stable operation and high quality of the transmission system. In modern industrial manufacturing, its application in automobile manufacturing, precision instruments, industrial equipment and other fields has significantly improved the overall quality.
2025-06-28
Automotive precision parts processing: Use high-precision gears to drive the future of new energy
The development of new energy vehicles has put forward higher requirements for the precision of parts. The breakthrough of micron-level manufacturing technology has laid the foundation for the stable operation of the power system. High-precision gears are innovatively applied in the energy conversion system of new energy vehicles, which reduces friction loss, improves transmission efficiency and prolongs gear life.
2025-06-18
The manufacturing process of precision accessories in modern medical equipment, especially the use of core processing technologies such as CNC turning and laser micro-welding to achieve precise manufacturing in complex medical scenarios. These technologies not only require precise dimensional control, but also must meet biocompatibility and long-term stability.
2025-06-14
Five-axis machining centers have gradually become the core equipment for the manufacture of complex parts due to their multi-dimensional dynamic machining capabilities. Compared with four-axis equipment, five-axis machining centers significantly improve the machining accuracy and surface quality of special-shaped structural parts through multi-angle synchronous cutting, shortening the production cycle.
2025-06-11