The influence of tool coating on machining surface quality in machining
Release time:
2025-02-27
Tool coating is a key factor in improving machining quality. It can significantly reduce the friction coefficient between the tool and the workpiece and increase the service life of the tool. At the same time, it has good wear resistance and corrosion resistance, and can effectively protect the tool matrix.
In the field of machining, the quality of the machining surface is directly related to the performance and service life of the product. Tool coating, as a key factor in improving machining quality, is receiving increasing attention. Whether in the pursuit of extreme precision in precision machining or in complex machining processes such as CNC milling and milling, tool coating plays an important role.
Working principle of tool coating
Tool coating is to coat one or more layers of thin films with special properties on the surface of the tool substrate. This film is like putting a layer of "protective clothing" on the tool, which mainly plays the following key roles. On the one hand, it can significantly reduce the friction coefficient between the tool and the workpiece. During the machining process, the tool is in close contact with the workpiece, and friction will generate a lot of heat, while the coating can reduce this friction and reduce the generation of cutting heat. On the other hand, the coating has good wear resistance and corrosion resistance, which can effectively protect the tool substrate and extend the service life of the tool.
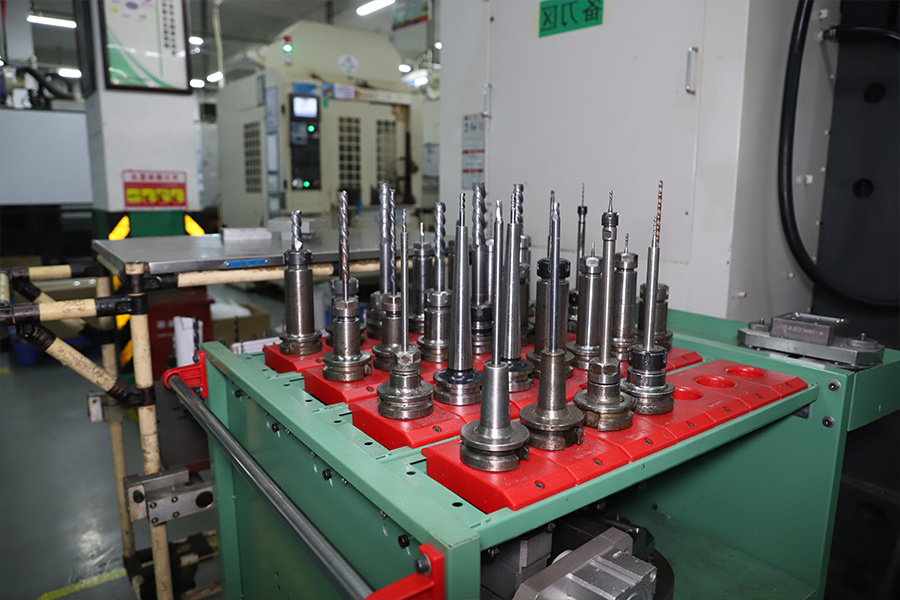
Effect of different coating materials on machining surface quality
- Hard coating: such as titanium nitride (TiN) coating, is a common hard coating. In CNC milling, TiN coated tools have high hardness and wear resistance, and can maintain the sharpness of the tool during high-speed cutting. Due to its low friction coefficient, it can reduce the fluctuation of cutting force, making the machined surface smoother and reducing surface roughness. For example, when machining aluminum alloy parts, TiN coated tools can effectively avoid adhesion between the tool and the aluminum alloy material, ensuring the quality of the machined surface.
- Lubricating coatings: such as molybdenum disulfide (MoS₂) coatings, which have excellent lubrication properties. In precision machining, when the surface quality requirements are extremely high, MoS₂ coatings can further reduce the friction between the tool and the workpiece, and reduce vibration and scratches during machining. Especially in turning and milling composite machining, which involves the switching of multiple machining processes, MoS₂ coatings can better adapt to complex machining environments and ensure the flatness and finish of the machined surface.
- Heat-resistant coatings: such as aluminum oxide (Al₂O₃) coatings, which have good thermal insulation properties and high temperature stability. In processing scenarios that generate a lot of heat, such as high-speed cutting and heavy cutting, Al₂O₃ coating can effectively block the transfer of cutting heat to the tool substrate, preventing the tool from wearing and deforming due to overheating. This is crucial to ensure the dimensional accuracy and shape accuracy of the machined surface. In machining, it can effectively avoid machining errors caused by thermal deformation of the tool and improve the quality of the machined surface.
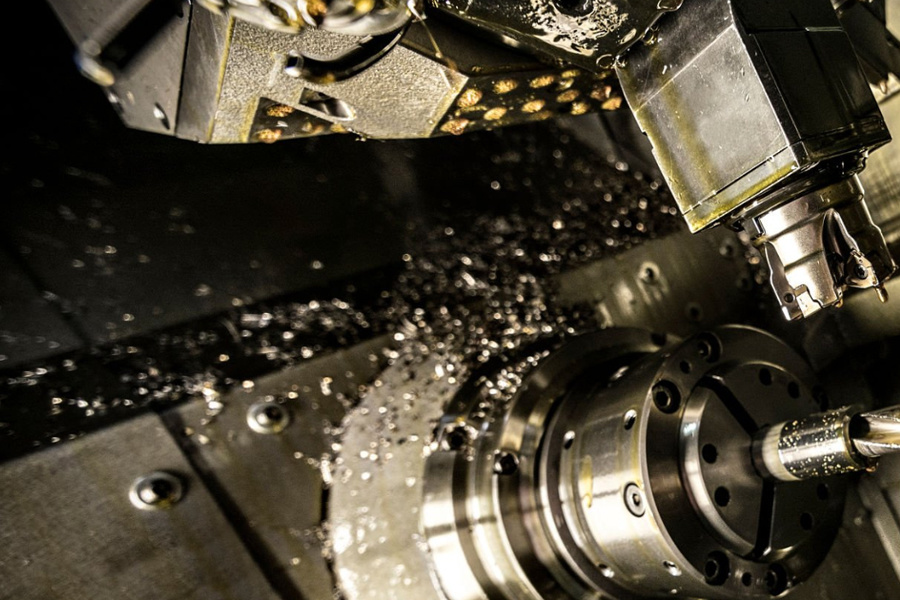
Tool coating has a positive impact on the quality of the machined surface in many aspects during machining. By selecting appropriate tool coating materials and processes, whether in CNC milling, turning and milling, or precision machining, the quality of the machined surface can be significantly improved, the surface roughness can be reduced, the dimensional accuracy and shape accuracy can be guaranteed, and the tool life can be extended, thereby improving production efficiency and product quality, and meeting the strict requirements of different industries for machining. With the continuous development and innovation of coating technology, it is believed that tool coating will play a greater role in the field of machining.
Related Products
CNC machining multi-axis linkage accurately processes tooth profile and journal size
CNC machining technology plays a core role in the machining of precision gears and shaft parts, achieving high-precision micron-level precision, significantly improving the wear resistance and fatigue resistance of parts, and ensuring the stable operation and high quality of the transmission system. In modern industrial manufacturing, its application in automobile manufacturing, precision instruments, industrial equipment and other fields has significantly improved the overall quality.
2025-06-28
Automotive precision parts processing: Use high-precision gears to drive the future of new energy
The development of new energy vehicles has put forward higher requirements for the precision of parts. The breakthrough of micron-level manufacturing technology has laid the foundation for the stable operation of the power system. High-precision gears are innovatively applied in the energy conversion system of new energy vehicles, which reduces friction loss, improves transmission efficiency and prolongs gear life.
2025-06-18
The manufacturing process of precision accessories in modern medical equipment, especially the use of core processing technologies such as CNC turning and laser micro-welding to achieve precise manufacturing in complex medical scenarios. These technologies not only require precise dimensional control, but also must meet biocompatibility and long-term stability.
2025-06-14
Five-axis machining centers have gradually become the core equipment for the manufacture of complex parts due to their multi-dimensional dynamic machining capabilities. Compared with four-axis equipment, five-axis machining centers significantly improve the machining accuracy and surface quality of special-shaped structural parts through multi-angle synchronous cutting, shortening the production cycle.
2025-06-11