Five-axis linkage machining center: the revolution of precision machining from three-axis to multi-axis linkage
Release time:
2025-04-24
This article introduces the definition, machining capabilities, typical applications and other dimensions of machining centers with different numbers of axes in detail, and focuses on revealing how five-axis linkage technology breaks through the geometric limitations of traditional machining through the characteristics of multi-axis linkage, and becomes a key equipment in high-end manufacturing fields such as aerospace, precision molds, and medical equipment.
In the field of precision manufacturing, the number of axes of a machining center is not only a symbol of technical strength, but also directly determines the processing capability of complex parts. From the basic three-axis machining center to the advanced four-axis, and then to the five-axis linkage machining center representing the top level of the industry, each breakthrough in the number of axes is accompanied by the innovation of processing technology. This article will systematically analyze the core differences of machining centers with different numbers of axes from the dimensions of axis definition, processing capability, typical applications, etc., and focus on revealing how the five-axis linkage technology breaks through the geometric limitations of traditional processing through the multi-axis linkage characteristics, and becomes a key equipment in high-end manufacturing fields such as aerospace, precision molds, and medical equipment.
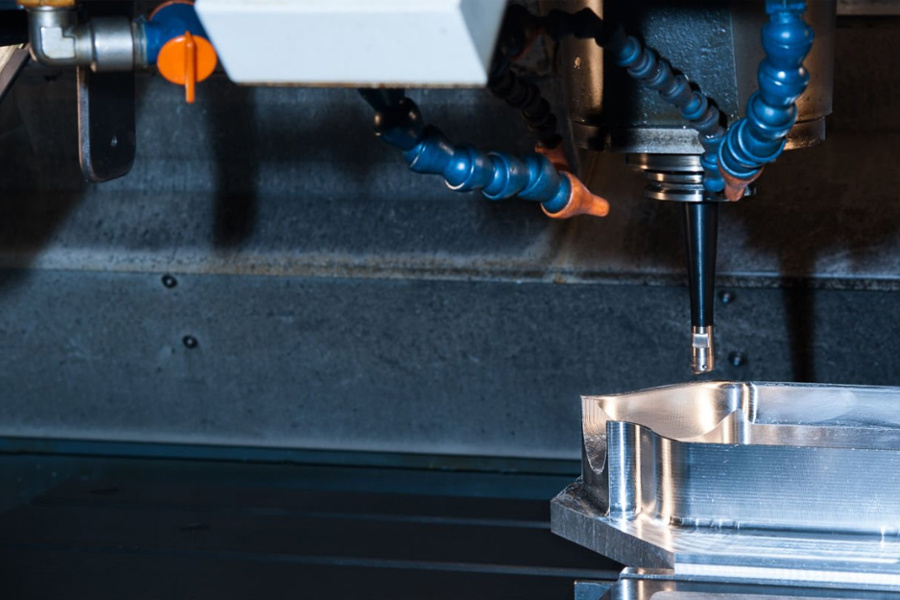
Axis definition: a technological leap from three-dimensional space to posture control
● Three-axis machining center: basic configuration for plane machining
The three-axis machining center (X/Y/Z linear axis) is the most common CNC machine tool. It realizes three-dimensional spatial positioning through the linkage of three linear axes. It is mainly used to process structures such as planes, grooves, and simple curved surfaces. Its advantages are relatively simple programming and low equipment cost, which is suitable for batch processing of flat parts. However, it also has obvious defects: the tool axis is fixed perpendicular to the workpiece surface, and the workpiece clamping needs to be adjusted multiple times when machining complex curved surfaces, which easily leads to the accumulation of precision errors, and special geometric features such as undercuts and deep cavities cannot be machined.
● Four-axis machining center: three-dimensional machining with added rotary axis
The four-axis machining center adds a rotary axis on the basis of three axes to realize rotary machining around a single axis. For example, the rotary axis can drive the workpiece to tilt, so that the tool can approach the workpiece at different angles, which enables the machining center to have the ability to machine features such as cones, bevels, and indexing holes, and is suitable for parts with rotationally symmetrical structures such as gearboxes and impellers. However, four-axis machining is still limited to a single rotary axis, and the tool posture adjustment range is limited. When machining complex free-form surfaces, it still needs to be carried out in sections.
● Five-axis linkage machining center: all-round control of dual rotary axes
The five-axis linkage machining center adds two rotary axes on the basis of three linear axes to realize five-axis linkage control. These two rotary axes can be worktable rotation or tool rotation, so that the tool axis can be adjusted at any angle in space. For example, when machining aero-engine blades, the tool can adjust its posture in real time along the normal direction of the blade surface, always maintaining the best cutting angle. This "tool-workpiece posture linkage" capability is the core advantage of five-axis technology compared to three-axis and four-axis technology.
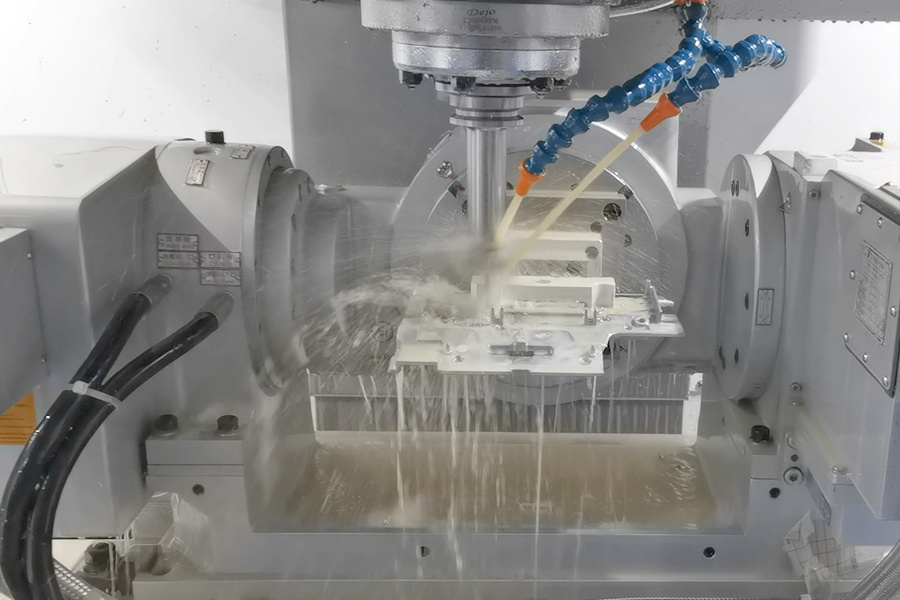
Machining capability comparison: geometric breakthrough from simple to complex
Three-axis machining centers mainly deal with planes and simple surfaces, and are often unable to do so when machining complex structures; four-axis machining centers expand the machining dimension through a single rotating axis, but still have limitations when facing complex free-form surfaces. In contrast, the advantages of five-axis linkage machining centers are very significant. Taking mold machining as an example, when a three-axis machine tool processes the convex and concave molds of automobile cover molds, the processing of the bottom of the deep cavity is more difficult; while a five-axis machine tool can swing the spindle head and cut in at a suitable inclination angle, which not only reduces the length of the cutting path, but also prolongs the tool life.
In terms of precision and efficiency, five-axis machining completes multi-faceted machining through one clamping, avoiding the errors caused by multiple positioning, and is particularly suitable for precision parts such as medical joint prostheses with extremely high precision requirements. When processing aluminum alloy structural parts for aerospace, the five-axis machine tool adopts a special milling strategy, which can effectively reduce air cutting and greatly shorten the processing time.
Core technical advantages: three disruptive values of five-axis linkage
1. Tool posture optimization: breaking through the limitations of cutting mechanics
In traditional 3-axis processing, errors are prone to occur when the tool cuts the surface vertically; while the five-axis machine tool can not only reduce the surface roughness, but also reduce the cutting force by adjusting the tool inclination angle, effectively avoiding the deformation of thin-walled parts, which is crucial for the processing of medical device components.
2. Complex structure one-time molding: subverting the traditional processing process
Take the inclined top mechanism in the injection mold as an example. The three-axis processing needs to be divided into multiple processes, which takes a long time; the five-axis machine tool can directly mill out the complex structure through the spindle head swing, greatly compressing the processing time, and avoiding the errors caused by other processing methods. This advantage is also very prominent in the processing of complex cavity parts in aerospace.
3. Flexible manufacturing adaptation: economic breakthrough in small batch production
For multi-variety small batch production, the five-axis machine tool has strong program versatility. When replacing similar parts for processing, only the parameters of the rotary axis linkage need to be adjusted, and there is no need to redesign the fixtures, which greatly shortens the changeover time. Combined with the automatic tool changing system, long-term unattended processing can also be achieved, significantly improving the utilization rate of equipment.
From three-axis plane processing to five-axis full-space precision manufacturing, the evolution of the number of axes in the machining center is not only an improvement in technical parameters, but also an innovation in manufacturing concepts. Five-axis linkage technology breaks through the geometric limitations and efficiency bottlenecks of traditional processing through tool posture control, one-time molding capabilities, and flexible production adaptation, and becomes the core support for high-end equipment manufacturing. For enterprises, choosing three-axis, four-axis or five-axis equipment requires comprehensive consideration of factors such as processing complexity, precision requirements, and production batches. With the advancement of Industry 4.0, the deep integration of five-axis machine tools with AI programming and IoT monitoring will further release the potential of multi-axis linkage processing and promote precision manufacturing into a new stage of development.
Related Products
CNC machining multi-axis linkage accurately processes tooth profile and journal size
CNC machining technology plays a core role in the machining of precision gears and shaft parts, achieving high-precision micron-level precision, significantly improving the wear resistance and fatigue resistance of parts, and ensuring the stable operation and high quality of the transmission system. In modern industrial manufacturing, its application in automobile manufacturing, precision instruments, industrial equipment and other fields has significantly improved the overall quality.
2025-06-28
Automotive precision parts processing: Use high-precision gears to drive the future of new energy
The development of new energy vehicles has put forward higher requirements for the precision of parts. The breakthrough of micron-level manufacturing technology has laid the foundation for the stable operation of the power system. High-precision gears are innovatively applied in the energy conversion system of new energy vehicles, which reduces friction loss, improves transmission efficiency and prolongs gear life.
2025-06-18
The manufacturing process of precision accessories in modern medical equipment, especially the use of core processing technologies such as CNC turning and laser micro-welding to achieve precise manufacturing in complex medical scenarios. These technologies not only require precise dimensional control, but also must meet biocompatibility and long-term stability.
2025-06-14
Five-axis machining centers have gradually become the core equipment for the manufacture of complex parts due to their multi-dimensional dynamic machining capabilities. Compared with four-axis equipment, five-axis machining centers significantly improve the machining accuracy and surface quality of special-shaped structural parts through multi-angle synchronous cutting, shortening the production cycle.
2025-06-11